УНИВЕРСАЛЬНЫЕ ДУГОВЫЕ ПЕЧИ ПОСТОЯННОГО ТОКА НОВОГО ПОКОЛЕНИЯ (ДППТУ-НП)
В.С. МАЛИНОВСКИЙ, к.т.н., президент ООО «НТФ «ЭКТА»
В металлургическое и литейное производства пришел новый вид плавильного оборудования - дуговые печи постоянного тока нового поколения (ДППТНП), позволяющий совершенствовать действующие технологии и создавать новые. Печи разработаны в России специалистами научно-технической фирмы «ЭКТА» в содружестве с рядом ведущих отечественных организаций. Новые печи, электротехнологические процессы в них запатентованы и не имеют мировых аналогов по технико-экономическим и экологическим параметрам при производстве стали, чугуна, сплавов на основе алюминия, никеля, кобальта, меди.
НТФ «ЭКТА» разработала комплексную систему плавки, в которой использование дуги постоянного тока является одним из важных, но не единственным элементом процесса. В ДППТНП использованы современные достижения силовой и управляющей электроники, результаты исследований физики дугового разряда, магнитной гидродинамики, металлургической теплотехники, теории металлургических процессов и основное оборудование с необычно широкими технологическими возможностями, в котором новые конструктивные элементы, режимы работы и процессы образуют единый эффективно действующий комплекс.
В ДППТНП удалось устранить практически все основные недостатки традиционных печей и расширить сферу эффективного применения дугового нагрева в литейном производстве.
При разработке механической части ДППТНП использованы все основные элементы дуговых печей переменного тока, по которым накоплен большой опыт производства и эксплуатации.
При плавке в ДППТНП могут быть использованы все известные технологические приемы: кип ванны, обработка шлаком, продувка металла кислородом или инертным газом, легирование и процессы, усиленные и ускоренные применением электромагнитного перемешивания.
Система МГД-перемешивания расплава
Разработанная система перемешивания расплава в ДППТНП за счет взаимодействия тока, протекающего через расплав, с электромагнитным полем протекающего тока, обеспечила не только равномерное распределение температуры и химсостава расплава, быстрое растворение легирующих элементов и большую эффективную поверхность взаимодействия расплава и шлака, но и позволила впервые эффективно обеспечить передачу энергии из дуги в расплав, осуществить защиту подины и подовых электродов от воздействия скоростных вихревых потоков в расплаве.
В результате ДППТНП имеет совершенную систему перемешивания расплава, которая с большой скоростью, непрерывно во все периоды нагрева и рафинирования расплава, выравнивает его температуру и химический состав, многократно увеличивает взаимодействие шлака и расплава, обеспечивает в полной мере передачу энергии электрической дуги в расплав практически без его локального перегрева. Новая система перемешивания расплава не имеет мировых аналогов, она предельно проста конструктивно и принципиально эффективнее перемешивания за счет бегущего магнитного поля, продувки металла кислородом, подачи газа через подину, внешнего магнитного поля и других известных способов.
Одним из важнейших следствий введения новой системы перемешивания связанной со специальной организацией режимов плавления явилось резкое снижение расхода электроэнергии при выплавке тонны металла без использования дополнительных источников энергии. На ДППТНП работающей в равных условиях с новейшими индукционными печами он всегда будет меньше, не менее чем на 15-20 %.
Энергетика процесса
В случае применения ДППТНП ударный характер нагрузки на питающую электросеть практически устранен. Соотношение номинальных мощностей сетевых и печных трансформаторов могут быть приняты 1,15-1,25, что существенно снижает установленную мощность сетевого оборудования при новом строительстве и не создает проблем при модернизации действующих печей с увеличением их производительности.
ДППТНП практически не создает резко-переменной нагрузки. Это достигается соответствующим специальным регулированием тиристорного преобразователя источника питания печи во все периоды плавки, стабилизацией тока дуги с заданной точностью оптимизированной для каждого периода плавки.
В ДППТНП режим ведется таким образом, чтобы мощность, потребляемая из сети, практически оставалась неизменной на всех этапах. Достигается это изменением схемы соединения тиристорных мостов (последовательное, последовательно-параллельное, параллельное). Таким образом, согласованное изменение напряжения и тока дуги в четыре раза не приводит к изменению мощности дуги, что позволяет полностью отказаться от регулирования мощности компенсирующих устройств. Кроме того, существенно меняются требования к регулированию вторичного напряжения печного трансформатора. Печной трансформатор выполняется только с ПБВ ±2,5 %.
При этом снижаются габаритная мощность и цена трансформатора.
Несмотря на более высокую стоимость источника электропитания ДППТНП, стоимость оборудования электропитания новой печи может быть ниже стоимость электрооборудования широко распространенных дуговых печей переменного тока (ДСП), так как применительно к печному агрегату, его нельзя рассматривать изолировано от системы электроснабжения. При выборе оборудования, сопоставления ДСП и ДППТНП должны выполняться комплексно с учетом всех сопутствующих факторов. При этом дополнительные капитальные вложения в систему электроснабжения ДСП практически компенсируют (в ряде случаев существенно превышают) стоимость источника питания ДППТНП.
Система управления
Для управления механизмами печи, кроме механизма перемещения электрода, применяется система, принятая для печей переменного тока. Сохраняется полностью также система контроля и блокировок, в которую добавляются цепи контроля за состоянием подовых электродов и соответствующие блокировки.
Система управления электрическим режимом кардинально отличается от ДСП. В ДППТНП предусматривается независимое управление током и напряжением дуги, обеспечивающее реализацию концепции ведения режима плавки: перемешивание расплава, защиту футеровки, снижение угара металла, пылегазо-выбросов и шума, генерируемого печью во все периоды плавки, а также колебаний мощности нагрузки.
Особенности процесса плавки
Процесс плавки разделен на три периода, которые проводят на постоянной мощности дуги.
Период 1 - подготовительный. Его проводят на высоком напряжении и небольшом токе дуги. Режим дуги позволяет вести расплавление шихты без привязки анодного пятна на расплав. Длинная дуга обеспечивает стабильный электрический режим, интенсивный нагрев печных газов, плавный нагрев всего объема шихты. Локальный перегрев металла не возникает, так как капли металла, нагреваясь, преодолевают силы поверхностного натяжения и немедленно стекают вниз. В этом периоде отгоняются органические загрязнения шихты, которые не разбавлены продуктами сгорания газа, шихты, подсосами воздуха в печь, как это происходит в ДСП. Эти испарения выходят из отверстия в своде и догорают до завершенных оксидов. Колебания активной мощности по сравнению со средним значением не превышают ± 10-20 %. Колебания давления в печи за счет стабилизации электрического режима подавлены, подсоса воздуха в печь не наблюдается. В течение периода 1 в шихте образуется расширяющаяся вверх воронка, которая в периоде 2 исключает обрушивание шихты на сводовый электрод и замораживание металла на подине.
В отличие от ДСП, энергосодержание отходящих газов зависит только от загрязненности шихты и обычно не превышает 0,5-0,8 % от подведенной мощности и утилизация их энергии нецелесообразна.
Период 2 - энергетический. В этот период обеспечивается стабильный электрический режим при колебании мощности не более ± 5 %, что способствует быстрому расплавлению шихты и не приводит к заметному локальному перегреву металла. Ток дуги в этот период удваивают, а напряжение в 2 раза снижают. В начале периода 2 анодное пятно дуги располагается на расплаве. Основная мощность дуги излучением и конвекцией печных газов передается в нерасплавленную шихту и через анодное пятно в расплав. Перегрев расплава под дугой в периодах 2 и 3 предотвращается соответствующим размещением подовых электродов, формирующим тороидальное вращение металла в вертикальной плоскости, при котором поток металла с большой скоростью подтекает под дугу и уходит вглубь расплава. В этих условиях температурное поле расплава выравнивается из-за интенсивной конвективной теплопередачи через расплав, а высокая скорость движения металла под дугой не допускает его локального перегрева. Снижению удельного теплового потока через анодное пятно дуги способствует низкая плотность тока в нем и наличие шлакового покрова. Во всех периодах плавки происходит минимальный угар металла, не образуется первичный шлак. В этих условиях состав шлака и его активность можно регулировать подачей шлакообразующих элементов. Образованный шлак жидкопод-вижен и из-за интенсивного перемешивания металла эффективно взаимодействует с расплавом.
Период 3 - технологический. Третий режим проводится на короткой дуге. Напряжение на дуге в четыре раза меньше, чем в 1 режиме, а сила тока в четыре раза больше. При этом происходит доплавление шихты, нагрев расплава, рафинирование и перемешивание расплава и шлака. В этот период можно проводить окислительный процесс подачей кислорода или рудным кипом, который при принудительном перемешивании металла весьма эффективен.
В процессе рафинирования нагрев металла ведется на полной мощности при коротких включениях дуги. Доля энергии, передаваемой в этот период непосредственно от дуги к расплаву, превышает 80 % подведенной. Интенсивная теплопередача от дуги к расплаву реализуется при усиленном воздействии поля электромагнитных сил на расплав. Этому способствует специальная схема размещения подовых электродов и токоподводов к ним.
Скорость тепло-передачи от дуги к расплаву увеличивается пропорционально росту силы тока. Это позволяет поддерживать оптимальный механизм плавления в широком интервале подводимой удельной мощности (от 0,3 до 8 кВт/кг шихты) в печах малой, средней и большой емкости, обеспечивая их высокую производительность.
В печах малой и средней емкости продолжительность расплавления ограничивается только технико-экономической целесообразностью и может составлять 10-15 мин. Скорость расплавления в ДППТНП большой емкости ограничивается только теплопроводностью массивных кусков шихты и экономичной мощностью источников электропитания. В печах емкостью 50-100 т продолжительность расплавления шихты может составить 30-40 мин. При работе ДППТНП в паре с установкой печь-ковш основное легирование расплава целесообразно проводить в ДППТНП, т.к. усвоение легирующих элементов в ДППТНП выше, чем в печи-ковше, а расход энергии для легирования ниже. В дуговых миксерах используются режимы третьего периода, обеспечивающие нагрев и рафинирование расплава, скорость нагрева ограничивается только технико-экономическими показателями и составляет 10-20 0С/мин. По специальному требованию Заказчика она может быть увеличена до 60-80 0С/мин путем установки источника электропитания повышенной мощности и форсирования перемешивания расплава.
Экология процесса
ДППТНП позволяет либо отказаться от системы пылегазоочистки, так как выбросы становятся ниже уровней ПДВ и ПДК или резко сократить ее производительность. При работе ДППТНП в 7-10 раз уменьшаются пылегазовыбросы в процессе расплавления шихты при значительном уменьшении угара металла. Это происходит при отсутствии принудительной прокачки воздуха через печь. При введении рудного кипа интенсивные пылевыбросы также отсутствуют, а образующаяся моноокись углерода догорает до СО2 при выходе из печи.
Поэтому в своде печи выполняется второе отверстие, через которое из печи свободно выходят образующиеся при плавке газы, которые забираются установленным над печью зонтом и поступают в систему вентиляции. Выбор производительности системы пылегазоулавливания зависит от качества шихты, технологического процесса и производится для конкретных условий.
После перевода дуговых печей переменного тока ДС-5МТ на питание постоянным током на ОАО «Кур-ганмашзавод» при увеличенной производительности печей пылегазовыб-росы оказались ниже ПДВ и ПДК при плавке стали 110Г13Л, чугуна, конструкционных и нержавеющих сталей. При интенсивном окислительном процессе, проводимом после расплавления шихты, объем отходящих газов и содержание пыли в нем зависит только от количества примесей в распла ве, которые перед началом окисли
тельного процесса следует определить и оптимизировать темп их окисления,
сдерживая тем самым чрезмерное образование пыли и газов. Окислительный период в завершающей стадии расплавления позволяет экономить электрическую энергию, однако эта экономия себя не окупает, если достигается за счет угара полезных состав
ляющих шихты. В ДППТНП при использовании качественной шихты окислительный период может не проводиться, в этом случае производительность системы пылегазоудаления определяется требованиями первого периода.
Значительным преимуществом ДППТНП является отсутствие заметных тепловых потерь (0,3-0,7 %) с отходящими газами. Это удешевляет систему пылегазоочистки и позволяет повысить ее эффективность.
При плавке цветных металлов вредное влияние на экологию при получении высококачественного литья уменьшается за счет резкого уменьшения испарения цветных металлов и их угара. При плавке сплавов на основе алюминия или переработке вторичного сырья высокое качество металла связанное с глубоким удалением газов и неметаллических включений достигается без использования хлоро- и фторосодержащих флюсов.
ДППТНП представляют уникальную возможность многим предприятиям России решить экологические проблемы действующих ДСП с коротким сроком окупаемости затрат на эти цели. Причем объем капитальных затрат на реконструкцию может быть ниже затрат на строительство систем пылегазоочистки для действующих ДСП, которые экономически только снизят рентабельность производства.
Уникальные возможности ДППТНП
Начало промышленному освоению ДППТНП было положено на Ков-ровском электромеханическом заводе в 1987 году пуском печи ДППТ-0,5 емкостью 0,5 т, которая заменила четыре индукционно-тигельные печи ИАТ-0,4. К настоящему времени литейный цех предприятия оснащен двумя подобными печами и готовится к пуску третья. За 14 лет работы первой печи ни разу не проводилась замена футеровки печи. Печь работает по графику в одну – две смены с перерывами в периоды пиковой стоимости электроэнергии, в основном, для производства высококачественных отливок алюминиевого сплава AL-Si марки АК7ч, качество которого полностью удовлетворяет требованиям ГОСТ 1583-93 и значительно превосходит его по механическим свойствам.
По экспериментальной программе были проведены многократные переплавы сплава АЛ9 с использованием 100 % чушек и 100 % возврата. При пятикратном переплаве химический состав и механические свойства на уровне предела прочности 172-175 МПа, относительного удлинения 4,1-4,6 %, твердости НВ 60-63 не изменились, а содержание водорода осталось в пределах 0,3 см3/100 г.
Специалистами Заволжского моторного завода на печи постоянного тока были проведены сравнительные плавки моторного лома сплава АК9ч, из которого не удаляли детали на основе железа. На основании исследования полученного сплава определили, что он полностью соответствует по химическому составу требованиям ГОСТ 1583-93 и значительно, в 1,5-2,0 раза, превышает требования к механическим свойствам. Плавка подобной шихты в серийной печи ИАК-2,5 привела к получению металла не соответствующего ни одному из показателей требований ГОСТа.
Анализ качества металла выплавляемого на всех ДППТНП, введенных в промышленное производство, указывает на очень высокий уровень показателей даже при использовании шихты невысокого качества.
На ДППТНП также отработаны технологии и была доказана возможность переплава стружки, шлаковых съемов, различных лигатур, крупногабаритного лома, выплавка которых ведется в диапазоне температур 650-1700 0С с очень высокими технико-экономическими показателями.
">Ключевые преимущества и достоинства ДППТНП:
· экологичность металлургических процессов;
· новый принцип магнитогидродинамического (МГД) перемешивания расплава;
· новые электрические режимы расплавления шихты, нагрева и рафинировании ярасплава;
· низкий расход электроэнергии;
· значительное повышение качества производимых металлов и сплавов без использования дополнительного оборудования;
· широкий диапазон номенклатуры выплавляемых металлов и сплавов;
· возможность вести плавку из дешевого сырья – за счет ведения активных технологических процессов;
· высокая производительность;
· низкий угар шихтовых материалов, графитированных электродов.
По желанию Заказчика НТФ «ЭКТА» может разработать ДППТНП любой емкости. Фирма имеет лицензии Госстроя и Госгортехнадзора России на право ведения всего объема проектно-конструкторских работ и поставку оборудования с дальнейшим шеф-монтажом и пусконаладкой.
С технологическими технико-экономическими параметрами печей можно познакомиться в НТФ «ЭКТА» и на предприятиях, на которых ДППТНП находятся в промышленной эксплуатации.
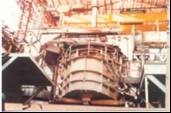
ДППТУ-24. Elektrotherm, Индия. Производство безникелевых нержавеющих сталей. Основная шихта - металлизированные окатыши.
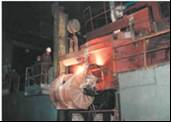
ЗАГ. ОАО «Мотордеталь», г. Кострома. Используется для безотходного переплава 100 % ДППТУ- чугунной стружки.
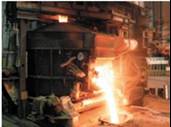
ДППТУ-6. ОАО «Металлургический завод «Электросталь». Реконструкция ДС-5МТ. Производство высоколегированных сталей и сплавов.
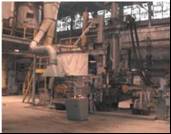
ДППТУ-12. ОАО «ГАЗ», г. Нижний Новгород. Выплавка синтетического чугуна и сталей для автомобильной промышленности
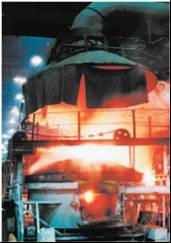
ДППТУ-6АГ. ОАО «Курганмашзавод» (реконструкция ДСП-5). Производство стали типа 110Г13Л, ХМЛ, 1Х18Н10Т, специальных и высокопрочных чугунов.