УНИВЕРСАЛЬНЫЕ ДУГОВЫЕ ПЕЧИ ПОСТОЯННОГО ТОКА НОВОГО ПОКОЛЕНИЯ ДЛЯ МЕТАЛЛУРГИИ И МАШИНОСТРОЕНИЯ
к.т.н. В. С. Малиновский,
В. Д. Малиновский,
И. Б. Власова (ООО «НТФ «ЭКТА»)
НТФ «ЭКТА» создала парк и освоила производство промышленных универсальных дуговых печей и миксеров постоянного тока нового поколения (ДППТУ-НП и ДМПТУ-НП), которые успешно эксплуатируются на многих предприятиях России и зарубежья.
Универсальные дуговые печи постоянного тока нового поколения (ДППТУ-НП) вместимостью от 0,5 до 100 т и дуговые миксеры постоянного тока (ДМПТУ-НП) вместимостью до 150 т предназначены для производства качественного литья и переработки лома рядовых и высоколегированных марок стали, чугуна, включая серый и весь ряд марок высокопрочных и легированных чугунов, синтетического чугуна, сплавов на основе алюминия, меди, никеля, кобальта, свинца и др. металлов, а также для производства любых лигатур на основе перечисленных металлов, ферросплавов, раскислителей и других материалов. В ДППТУ-НП и ДМПТУ-НП введен комплекс новых технических решений, который позволил значительно расширить технологические возможности дугового нагрева и устранить главные недостатки дуговых печей.
Печи и миксеры - универсальны, так как предназначенные для плавки различных металлов, они не отличаются друг от друга по конструкции и применяемым огнеупорным материалам. Это создает возможности производства широкого спектра сортамента и легкий переход с одного сортамента на другой. При этом ДППТУ-НП позволяют переплавлять любые виды шихты без специальной подготовки, включая стружку.
Для переработки металлолома эффективно использование комбинацию ДППТУ-НП небольшой емкости, с высокой скоростью плавления, и ДМПТУ-НП, вместимость которого значительно превышает вместимость ДППТУ-НП. Такая комбинация оборудования особенно эффективна при переработке легированного стального лома, сплавов на основе Al и Cu. Плавильная печь в такой установке позволяет провести качественную сортировку лома с точным определением его химического состава, принять решение о возможности использования расплава для приготовления конкретного сплава в миксере. Металл с большими отклонениями от требований хим.состава сплава отливается в шихтовую болванку и используется для подшихтовки сплавов в миксере, химический состав которых соответствует составу шихтовой болванки.
Перспективной возможностью использования ДППТУ-НП является перевод дешевого лома в более дорогой шихтовой материал. Например, выплавка из стального лома синтетического чугуна с низким содержанием серы; производство сложных лигатур и раскислителей из алюминиевых отходов; производство ферротитана и других ферросплавов.
Печи поставляются в стандартной комплектации - источник питания, автоматическая система управления процессом плавки (АСУ-плавка) и автоматическая система технологическим процессом (АСУ ТП), плавильная емкость; и в агрегатном исполнении (ДППТУ-АГ) с двумя плавильными емкостями. В них можно вести переплав отличающихся друг от друга металлов. Емкости могут отличаться друг от друга вместимостью, одна из них может выполнять роль плавильной печи, с функцией сортировки лома, другая - функцию миксера.
Предприятия, оснащенные оборудованием ДППТУ-НП, ДППТУ-АГ и ДМПТУ-НП способны производить широкий сортамент высококачественного литья из любой шихты, в том числе из шихты низкого качества, и эффективно проводить переработку вторичного лома.
Кроме использования ДМПТУ-НП по прямому назначению - выдержки и нагрева расплава, сочетание ДППТУ-НП и ДМПТУ-НП позволяет оптимизировать многие технологические процессы. Так, для организации производства, где время от времени требуется получение отливок большой массы, целесообразно создание комплексов, в состав которых входят печи ДППТУ-НП небольшой емкости и миксеры ДМПТУ-НП в разы большей емкости. Необходимая электрическая мощность миксеров большой вместимости ДМПТУ-НП в разы меньше электрической мощности такой же вместимости плавильных печей. Это позволяет при основном производстве стального литья массой отливок, например, 5 тонн, получать при необходимости отливки массой 30 и более тонн, не увеличивая при этом энергоемкость предприятия.
Также, например, при производстве высококачественного алюминиевого литья из алюминиевого лома произвольного состава, целесообразно вести быстрое расплавление шихты в печах ДППТУ-НП небольшой емкости, а доведение сплава до необходимого химического состава и процесс рафинирования проводить в миксере. Плавильная печь обеспечивает, при этом, качественную сортировку лома, удаление неметаллических включений из расплава, его дегазацию, отделение от стальных и прочих приделок, а миксер - получение качественного с высокими свойствами литья.
Приведенные примеры показывают широкие возможности применения нового типа оборудования для организации ведения различных эффективных технологий.
В ДППТУ-НП введен комплекс новых технических решений, который позволил значительно расширить технологические возможности дугового нагрева и устранить главные недостатки дуговых печей.
Показатели ДППТУ-НП создали условия для высокорентабельной замены ДСП, индукционных и других плавильных печей на ДППТУ-НП. ДППТУ-НП могут быть созданы, в том числе, путем перевода ДСП на питание постоянным током.
Накопленный опыт промышленного освоения ДППТУ-НП, в отличие от других фирм, основан на анализе результатов эксплуатации реально действующих печей, созданных НТФ «ЭКТА», и, несомненно, представляет интерес для специалистов, работающих в области металлургии и машиностроения, а также в области металлургии и машиностроения.
Высокие качественные и технико-экономические показатели при производстве чугуна, сплавов на основе алюминия, меди, никеля, свинца, ферросплавов, раскислителей, лигатур и других металлов на ДППТУ-НП достигаются достаточно просто, и содержат, в той или иной мере, элементы технологий, применяемых в процессе плавки стали. Поэтому особенности ДППТУ-НП в настоящей статье в основном связаны с производством стали.
ДППТУ-НП созданы на основе новейших разработок в области металлургии, силовой электроники, систем микропроцессорного управления, магнитной гидродинамики, исследований в области дугового разряда и другого.
Начальная стадия разработки концепции ДППТУ-НП была осуществлена при подготовке реконструкции ДСП-30 ПО "Ижсталь" в дуговую печь постоянного тока ДСПТ-30 [1]. Концепция включала в себя создание источника питания, с последовательно-параллельным переключением секций тиристорного преобразователя, позволяющего начало плавки вести на пониженном токе и повышенном напряжении и продолжение плавки - на повышенном токе и пониженном напряжении. Это позволило значительно уменьшить угар шихты, пылегазовыбросы из печи, ускорить процесс плавки, создать благоприятные условия для улучшения качества металла. Промышленное освоение печи ДСПТ-30 полностью подтвердило соответствие поставленных целей и полученного результата [2].
В единую концепцию создания ДППТУ-НП, разработанную специалистами ООО «НТФ «ЭКТА», были включены специальные энерготехнологии. Они позволили в ДППТУ-НП не использовать альтернативные источники энергии, природный газ, кислород, угольный порошок и другие. От разработок дуговых печей других фирм они отличаются следующим.
Дуговые печи переменного тока и дуговые печи постоянного тока, разработанные за рубежом, имеют принципиальную схему, показанную на рис.1.
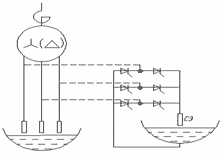
Рис.1 Принципиальная электрическая схема ДСП и ДСПТ |
В базовую схему ДСП входит печной трансформатор со ступенями переключения напряжения. На высокой стороне подключается реактор. Фазы трансформатора связаны с электродами дуговой печи переменного тока непосредственно, в дуговых печах постоянного тока зарубежного производства - через управляемый выпрямитель. В процессе плавки есть возможность управления напряжением - путем переключения ступенейнапряжения трансформатора и методом стабилизации и управления мощностью дуги - путем изменения длины дуги. В печи постоянного тока зарубежного производства имеется дополнительная возможность управления и стабилизации тока тиристорным регулятором. |
В вышеуказанных печах плавка обычно ведется на максимальном токе, определенном параметрами трансформатора.
Данная схема, рис.1, обеспечивает быстрое расплавление шихты в начальный период плавки при высоких значениях тока и напряжения электрических дуг. Затем мощность приходится снижать, т.к. футеровка печей не допускает работу на длинных дугах. Уменьшение напряжения сопровождается снижением вводимой в печь мощности, которая может быть компенсирована только применением тепла химических реакций, получаемого за счет использования различных видов горелок, кислорода и других методов. В современных печах для защиты футеровки используют "длинные" дуги, затопленные во вспененном шлаке. Проблема перемешивания расплава и передачи энергии в расплав решается путем продувки расплава кислородом или другими газами. В противном случае, доплавление шихты и нагрев расплава ведутся на пониженной мощности, и печь обладает малой производительностью. Все приемы форсирования плавки теплом химических реакций приводят к высокому (9-12 %) угару шихты и мощной нагрузке на систему пылегазоудаления.
В отличие от вышеуказанных печей, источник питания ДППТУ-НП разработки НТФ «ЭКТА» (рис.2) включает в себя трансформатор с несколькими трехфазными обмотками, каждая из которых подключена к секции тиристорного преобразователя. Через реакторы секции тиристорного преобразователя подключены к подовым электродам. В отличие от аналогии с автомобилем начала прошлого века, ДППТУ-НП оснащена не только "регулятором газа" - ступенчатым переключателем напряжения, но и "автоматической коробкой передач" - системой переключения секций тиристорного преобразователя [3, 4].
На источнике питания (рис.2) начало плавления ведется с последовательно включенными секциями тиристорного преобразователя (рис.3.) на пониженном токе и высоком напряжении, при включенном одном подовом электроде печи [3,4].
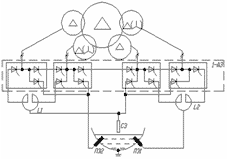
Рис. 2. Принципиальная схема источника питания ДППТУ-НП. |
В этот период плавка ведется на длинной дуге, и ее анодное пятно располагается на кусках металлической шихты. В этих условиях достигаются главные цели: 1. Не допускается перегрев расплава, т.к. расплавленные капли металла, нагреваясь, преодолевают силу поверхностного натяжения и стекают на подину печи. 2.Плавка ведется на стабилизируемой мощности практически без колебаний электрического режима. |
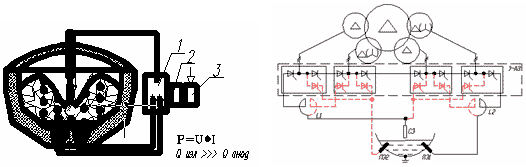 |
Рис. 3. Коммутация источника питания для расплавления шихты в течение первого периода плавки. 1 - Источник питания. 2 - Регулятор тока. 3 - Блок управления перемешиванием расплава. |
Второй период плавки ведется при коммутации секций тиристорного преобразователя: по две секции - параллельно и между собой - последовательно (рис.5). При этом ток дуги удваивается, а напряжение в два раза снижается, т.е. сохраняется мощность первого периода плавки. Для перемешивания накопленного в первый период расплава подключается второй подовый электрод [3, 4]. Анодное пятно дуги располагается на расплаве, накопленном при проведении первого периода, внутри воронки, проплавленной в шихте ранее. Для отвода мощности от анодного пятна расплава включается система перемешивания расплава. Согласно патентам [3, 4], перемешивание осуществляют периодическим изменением величины тока с одновременным изменением поля электромагнитных сил. При наличии нескольких замкнутых электрических цепей, изменение тока в них производят со сдвигом фаз в каждой цепи относительно другой.
При установленных в подине печи двух подовых электродах, смещенных относительно центра печи, вектор тока внутри расплава имеет горизонтальную и вертикальную составляющие. Взаимодействие вертикальной и радиальной составляющих тока с магнитным полем тока формирует поток расплава, при котором металл с большой скоростью набегает под пятно дуги и уходит вглубь расплава. По подобному типу формируется и горизонтальное перемешивание расплава. Это перемешивание идеально для передачи энергии дуги в расплав и для футеровки печи, поскольку вблизи футеровки печи скорость перемешивания металла минимальна. Однако, с течением времени характер перемешивания металла изменяется, в расплаве появляются вихревые потоки, а движение основной массы металла прекращается. Для предотвращения этого явления и управления скоростью и формой перемешивания металла регулятором тока тиристорного преобразователя, согласно патентам [3, 4], время от времени проводится кратковременное снижение тока, при котором вихревые потоки разрушают, и, восстанавливая регулярное перемешивание расплава. Перемешивание расплава не допускает локального перегрева металла под дугой, а образовавшаяся в течение первого периода воронка в шихте позволяет поддерживать высокую стабильность вводимой мощности.
Во второй период плавки ведут расплавление основной массы шихты, проведя соединение секций тиристорного преобразователя согласно рис. 4.
На рис. 5 (а, б, в) показаны также типы перемешивания расплава: рис.5(а, б) - с включенной системой перемешивания; рис. 5(в) - с отключенной. В последнем случае под анодным пятном дуги и над подовыми электродами формируются в расплаве вихри, при этом, движение основной массы расплава прекращается
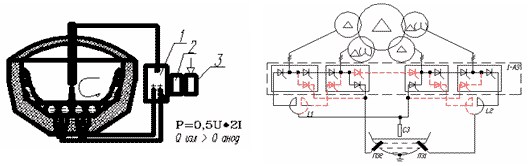 |
Рис. 4. Коммутация источника питания для расплавления шихты в течение второго периода плавки. 1 - Источник питания. 2 - Регулятор тока. 3 - Блок управления перемешиванием расплава.
|
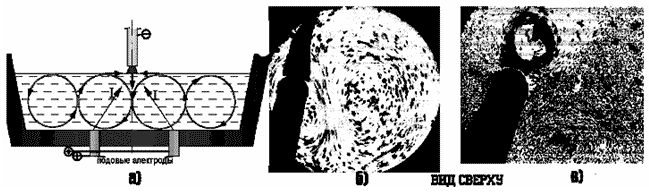 |
Рис. 5. Типы перемешивания расплава в ДППТУ-НП. а) Тороидальное перемешивание расплава. б) Регулярное перемешивание расплава. в) Искаженная система перемешивания с вихревыми потоками расплава. |
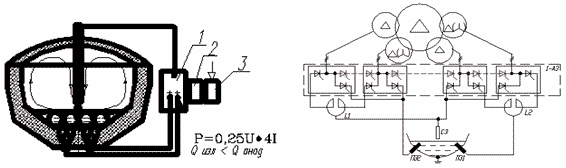 |
Рис.6. Коммутация источника питания для нагрева расплава и проведения технологических процедур. 1 - Источник питания. 2 - Регулятор тока. 3 - Блок управления перемешиванием расплава.
|
После расплавления основной массы шихты источник питания переключается для ведения третьего периода плавки (рис.6). Для этого, в соответствии с патентами [3, 4], все секции тиристорного преобразователя включаются параллельно.
В третьем периоде ток увеличивают в два раза - по сравнению со вторым периодом и в четыре раза - по сравнению с первым периодом плавки, а напряжение источника питания пропорционально увеличению тока снижается, т.е. вся плавка ведется при постоянной мощности с полным использованием силовых возможностей трансформатора. Увеличение тока приводит к увеличению интенсивности перемешивания расплава [3, 4], а энергия дуги перераспределяется. В отличие от первого и второго периодов, в которых основная доля энергии излучалась на шихту, доля энергии третьего периода (до 80-90 %) передается непосредственно в расплав, а система перемешивания переносит её вглубь расплава. Это позволяет отказаться от применения вспененного шлака, кислорода и других газов, используемых в ДСП и дуговых печах постоянного тока зарубежного производства для ускорения расплавления.
В ДППТУ-НП за счет перемешивания расплава достигаются большая эффективная площадь взаимодействия системы шлак-расплав, идеальная гомогенность температуры и химического состава расплава, быстрое растворение и высокое усвоение легирующих элементов, интенсивная скорость ведения технологических процессов: десульфурации, дефосфорации, науглероживания, обезуглероживания расплава, удаление неметаллических включений, дегазация расплава; минимальный удельный расход электроэнергии, сокращается угар шихты, гарантируется высокое качество металла.
Разработанная система плавки способствует, например, глубокому удалению водорода из алюминиевых сплавов. Результатом явились те показатели, которые были достигнуты на ДППТУ-НП. Организация передачи энергии из дуги в расплав обеспечивает минимальный расход электроэнергии на расплавление металла и, проведение технологических процессов обработки расплава. Для малых печей, с целью реализации идей патентов [3, 4], разработана принципиальная схема источника питания, при котором трансформатор имеет одну высоковольтную и, по крайней мере, две низковольтные обмотки. Высоковольтная обмотка обеспечивает ведение первого периода плавки, низковольтные - второго и третьего. При этом, соотношение тока и напряжения дуги первого, второго и третьего периодов может быть произвольным.
Энерготехнологии ДППТ-НП непосредственно связаны с экологией процесса плавки.
Выше отмечалось, что для организации и ускорения процесса плавки в ДППТУ-НП не применяются вспененный шлак, любые виды химических топлив и кислород. Это обеспечивает выполнение Киотских соглашений при минимальных затратах на систему пылегазоудаления и очистки.
На угар шихты в значительной мере играет газообмен печной среды с окружающим воздухом. Газообмен прямо связан с уровнем стабилизации электрического режима дуги.
В соответствии с уравнением PV=nRT, при постоянном объеме печи (V), давление в печи (P) является функцией температуры (T) газа внутри печи. При колебаниях электрического режима происходит изменение температуры газов печной среды, и печные газы выбрасываются из печного пространства или засасываются в него.
Этот режим характерен для ДСП и дуговых печей постоянного тока зарубежного производства, и устранен в ДППТУ-НП специальными, описанными выше, режимами плавки. Подавление газообмена позволило не осуществлять принудительной эвакуации газов из печи, резко снизить окисление металла поступающим в печь из воздуха кислородом, предотвратить насыщение металла азотом и кислородом. Также обеспечивается плавка в атмосфере газов, выделяемых из расплава, которые при плавке стали содержат большое количество СО.
При необходимости, атмосферой печи можно управлять, подавая в нее принудительно любые необходимые для ведения технологии газы.
Электрическая дуга постоянного тока является мощным насосом, прокачивающим через себя печные газы. При этом, температура печных газов внутри печи достигает высоких значений, превышающих 1000 °С. При таких температурах невозможно образование диоксинов, фуранов, цианидов, других вредных соединений. В первый период плавки органические и другие, загрязняющие шихту материалы, испаряются, нагреваются внутри печи до высокой температуры, а при выходе из печи - воспламеняются и окисляются до простых соединений. Небольшое количество образующихся газов и организованный интенсивный поток воздуха в отходящий из печи поток печных газов, обеспечивает высокую скорость горения печных газов и быстрое их охлаждение до температуры, как правило, ниже 100° С, т.е. обеспечивают наилучшие условия для предотвращения образования вредных химических соединений. Система организации плавки гарантирует удаление вредных соединений из шихты, позволяет не вести подготовку загрязненной шихты перед плавкой. Эти условия невозможно выполнить в других печах.
Во многих случаях ДППТУ-НП можно не оснащать системой пылегазоочистки. Это позволяет для ДСП вместо строительства дорогостоящей системы пылегазоочистки провести реконструкцию печи переменного тока с переводом на постоянный ток.
В таблице 1 приведены результаты замеров выбросов установки
ДППТУ-6АГ, которая была создана методом реконструкции ДСП-6, при плавке стали 110Г13Л, из чего следует, что поставленная задача была решена.
Выбросы, г/с |
ПДВ, г/c |
Пыль |
0,3301 |
0,9853 |
В т.ч. Mn |
0,0266 |
0,1486 |
|
Многократное уменьшение пылегазовыбросов отмечено на всех печах, введенных в производство НТФ «ЭКТА». Это является одним из главных достоинств ДППТУ-НП. |
Для условий России важно то, что ДППТУ-НП работают с полным сливом расплава, что де-лает безопасным использование влажной шихты.
Для металлургического оборудования важнейшее значение имеет его промышленная безопасность. В ДППТУ-НП она обеспечена следующими техническими решениями.
Основой механической части ДППТУ-НП является механическая часть ДСП с небольшими конструктивными изменениями. Подина печи футеруется обычными, разработанными для ДСП, основными, кислыми и другими огнеупорами. Часть кожуха, охватывающая подину печи, не имеет охлаждаемых элементов. Стены и свод печи могут быть охлаждаемыми, но при этом, водоохлаждаемые узлы всегда расположены над расплавом, и их разрушение не приводит к взрывам.
Особо следует остановиться на конструкции подового электрода.
Подовые электроды размещают внутри футеровки подины печи и обеспечивают подвод тока от источника питания к металлу. В процессе длительной промышленной эксплуатации применялись различные типы подовых электродов, но наилучшим, применяемым в ДППТУ-НП вариантом, явилась конструкция подового электрода, описанная в патенте РФ [5]. В конструкции подового электрода решены вопросы организации его производства, ремонта, надежности в эксплуатации, взрывобезопасности. Схема подового электрода представлена на рис. 7.
Подовый электрод представляет собой стальные листы, проходящие через подину печи, жестко скрепленные с токоподводом (базой), представляющим собой стальную трубу, внутренняя часть которой методом ЭШП заполнена медью. База размещена в нижней части футеровки вдали от её рабочей поверхности. Под корпусом печи выполнены каналы охлаждения. Внутри базы размещены датчики контроля температуры. Конструкция взрывобезопасна,поскольку каналы охлаждения вынесены за пределы печи, и состояние базы непрерывно контролируется [5].
|
При замене футеровки подовые электроды отделяются от базы, и к ней крепятся новые. Для гарантированно длительной работы подового электрода и контакта подового электрода с шихтой, организации полного слива расплава, нами разработан и запатентован ряд приемов.
Рис. 7. Подовый электрод с токоподводом (базой). 1- футеровка; 2- подовый электрод (ПЭ); 3.1, 3.2- база; 4- узел охлаждения; 5- кожух печи |
По уровню промышленной безопасности ДППТУ-НП не уступает ДСП и, безусловно, безопаснее индукционных плавильных печей, в которых охлаждаемые элементы и расплав отделены друг от друга относительно тонкой футеровкой.
Благодаря оригинальным техническим решениям резко расширены возможности дугового нагрева при плавке различных металлов, в частности, ДППТУ-НП позволяют на новом уровне осуществлять технологию производства стали, основанную на классической теории металлургических процессов.
Технологическая концепция выплавки качественных сталей в ДППТУ-НП принципиально отличается от концепции выплавки стали в дуговых печах постоянного и переменного тока, в массовом порядке принятой в мире в настоящее время.
Согласно принятой в мире концепции - в дуговой печи производится плавка шихты с применением дугового нагрева и альтернативной энергии - газокислородных горелок, кислородных ижекторов, инжектора углеродосодержащего порошка, использование вспененного шлака, работа на болоте.
Эти печи не позволяют выплавлять сталь заданного состава, но обеспечивают высокую скорость расплавления шихты и сниженный расход электроэнергии. Из такой печи металл передают в установку печь-ковш, в которой осуществляется процесс синтеза стали методами, принципиально отличающимися от классических методов сталеварения, широко описанных в теории металлургических процессов. С нашей точки зрения такая технология производства стали - является спорной, и мы видим в ней существенные недостатки, главный из которых - высокие затраты на получение высококачественной стали.
К ним относятся и недостатки комбинированной ДСП, в которой реализуется высокий угар шихты (8-15%), полный угар легирующих элементов шихты, специальные требования к переплавляемой шихте, высокое содержание кислорода и других растворенных газов в расплаве, а также наличие большого количества неметаллических включений в расплаве. Работа печи ДСП характеризуется массовыми выбросами с высокой энергоемкостью газов и пыли. В конечном итоге плавка шихты в комбинированных ДСП характеризуется высокими затратами на производство стали и сопровождается, даже при наличии дорогостоящей системы пылегазоочистки, интенсивными вредными газовыбросами в окружающую среду. Плавка в ДСП с высоким угаром шихты приводит к повышению содержания вредных элементов в расплаве, в частности Cu и Ni, которые не окисляются, при этом их содержание в расплаве растет пропорционально угару шихты.
Синтезирование стали в установках печь-ковш является тоже высоко затратным процессом, в котором кислородный или рудный кип (для перемешивания, дегазации и удаления неметаллических включений) заменен продувкой металла аргоном, и используются сложные дорогие методы раскисления, легирования и рафинирования стали, с целью получения заданных свойств.
В большинстве случаев повышение качества стали пытаются достигать с применением, дополнительно к установкам печь-ковш, установок вакуумирования металла в ковше.
Комплекс вспомогательных средств нагрева генерирует огромное количество отходящих газов и пыли, шум, многократно превышающий СНиП, приводит к очень значительным потерям металла. Для ДСП необходимо строительство шумозащитных боксов и мощной системы пылегазоочистки. Использование альтернативных видов энергии - не выгодно. Это легко определяется из показателей ДСП. К паспортному удельному расходу электроэнергии печи на плавку следует добавить расход электроэнергии в системе пылегазоочистки и в УПК. Следует пересчитать на стоимость электроэнергии расходные материалы: кислород, природный газ, шлакообразующие и, главное, - потери шихты и легирующих элементов шихты. Даже не учитывая затраты на транспортировку шлака, его переработку, транспортные расходы на сгоревшую шихту и другое, очевидно, что использование альтернативных видов нагрева увеличивает затраты на производство стали.
Без всякого сомнения, что эксплуатация и схема ДСП много сложнее
ДППТУ-НП.
Кроме того, система с ДСП включает в себя УПК, с низким ресурсом работы футеровки, достаточно сложными коммуникациями и установку вакуумирования ковша. При этом вопросы получения качественной стали остаются актуальными.
При производстве стали с невысокими требованиями к качеству, использование на финишных операциях процесса обработки металлов давлением «прячет» пороки металла, но это невозможно осуществить при производстве качественного литья.
Мы обращаем внимание на недостаточные исследования процесса синтезирования стали на ее наследственную структуру.
ДППТУ-НП - предусматривают ведение классических технологий, с полным циклом получения конечного продукта в ней.
ДППТУ-НП являются развитием классических ДСП. В них резко улучшены показатели плавки, в том числе связанные с повышением качества выплавляемой стали.
В ДППТУ-НП ведется: расплавление шихты, с наведением шлака заданного состава; окислительный и восстановительный процессы, причем окислительный процесс может проводиться как путем кислородного, так и рудного кипа; дефосфорация, десульфурация, легирование, рафинирование расплава, т.е. процессы, которые проводятся, в как в традиционных ДСП, так и в мартеновских печах.
В ДППТУ-НП процесс выплавки стали, по сравнению с ДСП, значительно усовершенствован и ускорен в стадии ведения технологических операций. Это является важнейшим достоинством ДППТУ-НП. Опыт промышленной эксплуатации ДПТУ-НП показал, что ведение в них одношлакового процесса с переносом технологических операций в установки печь-ковш, является серьезной ошибкой. В ДППТУ-НП целесообразно проводить полный цикл сталеварения. Так, нами в компании МАРДИА СТИЛ (Индия) была запущена в промышленную эксплуатацию ДППТУ-24, предназначенная для производства безникелевых нержавеющих сталей. По настоянию индийской стороны плавильный участок был оснащен установкой печь-ковш (УПК). В дальнейшем процессе производства стали она не участвовала, поскольку эффективность ведения технологий в ДППТУ-НП оказалась значительно выше и дешевле, чем в УПК.
Печи, предназначенные для ведения полного цикла, не могут характеризоваться малой продолжительностью плавки. Производство стали со стабилизированной структурой и высокая скорость процесса сталеварения, не обеспеченная специальными технологическими приемами, - несовместимы. По сравнению с ДСП в ДППТУ-НП за счет магнитогидродинамического (МГД) перемешивания расплава и других технико-энергетических приемов сокращается время ведения технологических операций. За счет этого появляется резерв времени для увеличения длительности расплавления шихты, т.е. возможность значительного снижения установленной мощности источника электропитания. Уменьшение времени ведения технологических операций в ДППТУ-НП намного превышает увеличение, по сравнению с ДСП, времени расплавления шихты. Это позволяет при реконструкции ДСП с переводом на постоянный ток в ДППТУ-НП практически удваивать производительность, без увеличения потребляемой мощности энергосистемы и значительно уменьшать удельный расход электроэнергии. Отказ от строительства мощных систем пылегазоочистки, подготовки шихты, внепечной обработки, фильтрокомпенсирующих устройств - приводит к сокращению в разы расходов на основные фонды, а эксплуатационные показатели обеспечивают быструю окупаемость этих затрат.
Требования, которые мы предъявляем к ДППТУ-НП, следующие: - технологические возможности должны обеспечивать производство высококачественной стали; - печная установка должна обеспечивать ведение классических технологических процессов производства стали; - технико-экономические показатели печей должны превышать показатели существующего печного парка; - угар металлической части шихты - не должен превышать 1,5%; - при переплаве легированной шихты, содержащиеся в ней легирующие элементы должны сохраняться; - воздействие на окружающую среду - минимально; - ведение плавки не должно характеризоваться резко-переменными нагрузками на систему электроснабжения, при практическом отсутствии фликера.
При согласовании плавильных мощностей с устройствами финишной обработки металла (МНЛЗ, прокатный стан, и т.д.) в отличие от принятых технических решений, в которых устанавливается одна печь, параметры которой должны быть четко согласованы с параметрами финишного оборудования (в том числе по производительности), в случае использования ДППТУ-НП требования к высокой производительности печи снимаются, но с параметрами финишного оборудования должны быть согласованы параметры плавильного участка, на котором, при необходимости, могут быть установлены несколько ДППТУ-НП. При этом выполняются высокие вышеперечисленные требования к показателям плавильного участка.
В целом, мы предлагаем следующую систему организации выплавки стали.
Технологические процедуры: расплавление, дефосфорация (при необходимости со сменой шлака), десульфурация, науглероживание (графитовая стружка), обезуглероживание (кислородный или, предпочтительнее, рудный кип), легирование, рафинирование, раскисление, управление температурой расплава. В течение плавки гарантируется гомогенность температуры и химического состава расплава шлака и металла.
Слив расплава - поворотом печи через сливной носок (сначала шлака, затем расплава). Это позволяет печной шлак (в ДППТУ-НП он высокого качества) использовать при продолжении рафинирования металла в разливочном ковше. Использование кислорода, газовых и других видов горелок, вспенивание шлака для защиты дуги с целью ускорения расплавления - не допускаются. Конструктивное использование плавильной емкости - футерованная подина, стены и свод - водоохлаждаемые. Система газоудаления - самопроизвольное истечение печных газов из второго отверстия в своде, забор через зонт в систему вентиляции. Удаление промежуточного шлака - через рабочую дверцу (возможно вспенивание шлака для его удаления).
В ДППТУ-НП устранены резкопеременные нагрузки, и не требуется усиленная система электроснабжения, практически устранен фликер, компенсация реактивной мощности решается простым методом. Трансформатор не оснащается устройствами РПН и ПБВ. Переключение режимов осуществляется бесконтактными тиристорными переключателями.
Система управления электрическими режимами позволяет вести всю плавку на постоянной мощности, обеспечить МГД-перемешивание расплава, является более простой по сравнению с системами управления ДСП. Заложенные в источник питания ДППТУ-НП возможности позволяют с высокой точностью стабилизировать ток и применять простые системы изменения напряжения - реализовывать технологические преимущества ДППТУ-НП, в т.ч. отказаться от дорогостоящей системы пылегазоочистки.
Таким образом, организация плавильных участков с ДСП значительно дороже и сложнее, чем с ДППТУ-НП, несмотря на обязательное использование тиристорного преобразователя и установку, при необходимости, нескольких ДППТУ-НП вместо одной ДСП.
Печи и миксеры (ДППТУ-НП и ДМПТУ-НП) - универсальны, так как предназначенные для плавки различных металлов, они не отличаются друг от друга по конструкции и применяемым огнеупорным материалам. Это создает возможности производства широкого спектра сортамента и легкий переход с одного сортамента на другой. При этом ДППТУ-НП позволяют переплавлять любые виды шихты без специальной подготовки, включая стружку.
Возможности ДППТУ-НП и ДМПТУ-НП, освоенные технологические процессы, их универсальность достоверно были подтверждены промышленной эксплуатацией оборудования НТФ «ЭКТА» на различных предприятиях в России и за рубежом, табл.1.
Универсальные дуговые печи и миксеры постоянного тока нового поколения
Тип печи |
Город, страна |
Предприятие |
Назначение оборудования |
ДППТУ-1,4АГ |
г. Ижевск, РФ |
ПО "Ижсталь" |
Высоколегированные стали и сплавы |
ДППТУ-0,5 |
г. Ковров, РФ |
ОАО "КЭМЗ" |
Производство высококачественного литья из алюминиевых сплавов. |
ДППТУ-30 |
г. Ижевск, РФ |
ПО "Ижсталь" |
Реконструкция ДСП-25. Производство инструментальной стали, типа Р6М5. |
ДППТУ-12 |
г. Набережные Челны, РФ |
ОАО "КАМАЗ" |
Производство стального литья. |
ДППТУ-6 |
г. Москва, РФ |
ОАО "ЗИЛ" |
Сталь, чугун для литья. |
ДППТУ-24 |
г. Ахмедабад, Индия |
"Elektrotherm" |
Производство безникелевых нержавеющих сталей. Основная шихта - металлизированные окатыши. |
ДППТУ-0,5 |
г. Екатеринбург |
ОАО "Уралмаш" |
Лигатуры для чугуна. |
ДППТУ-6АГ |
г. Курган, РФ |
ОАО "Курганмашзавод" |
Производство стали типа 110Г13Л, ХМЛ, 1Х18Н10Т, специальных и высокопрочных чугунов. |
ДППТУ-3АГ |
г. Воронеж, РФ |
ОАО "Рудгормаш" |
Производство стали, низко- и высоко-легированной, специальных видов чугуна. |
ДППТУ-3АГ |
г. Кострома, РФ |
ОАО "Мотордеталь" |
Используется для безотходного переплава 100 % чугунной стружки. |
ДППТУ-12 |
г. Н.Новгород, РФ |
ОАО "ГАЗ" |
Используется для выплавки синтетического чугуна и сталей для автомобильной промышленности. |
ДППТУ-12 |
г. Усолье Сибирское, РФ |
ОАО "ПО Усольмаш" |
Производство стали и чугуна. |
ДППТУ-0,5АГ |
г. Таллинн, Эстония |
"Aluminium alloys of Estonia AS" |
Производство на базе отходов алюминия высококачественных сплавов и всевозможных лигатур типа ALSi (10-60), AlFe (10-80), AlTi (5-70), AlMn и др. |
ДППТУ-20 |
г. Рязань, РФ |
ОАО "Тяжпрессмаш" |
Производство низколегированных и углеродистых сталей: ст.35, 4Х5МФС, 40Х, 40ХН2МЛ для качественного литья. |
ДППТУ-6 |
г. Бобруйск, Республика Беларусь |
ОАО "Бобруйский машиностроительный завод" |
Производство стали, низко- и высоко-легированной, специальных видов чугуна. |
ДППТУ-6 |
г. Электросталь, РФ |
ОАО "Электросталь" |
Выплавка высоколегированных марок стали и жаропрочных сплавов. |
ДППТУ-0,5АГ |
г. Ступино, РФ |
ОАО "Ступинская металлургическая компания" |
Выплавка алюминиевых сплавов под производство автомобильных дисков. |
ДМПТУ-12АГ |
г. Ярославль, РФ |
ОАО "Ярославский моторный завод" |
Миксеры для нагрева, выдержки и доводки чугуна, выплавляемого в вагранках, могут быть применены для получения стали, сплавов на основе алюминия, меди и т.д. Обладают возможностью ведения активных металлургических процессов. |
ДППТУ-6 |
г. Рязань, РФ |
ОАО "Тяжпрессмаш" |
Производство низколегированных и углеродистых сталей: ст.35, 4Х5МФС, 40Х, 40ХН2МЛ для качественного литья. |
ДППТУ-1,5АГ |
п. Верхне-Днепровский, Смоленская обл., РФ |
ОАО "Дорогобужкотломаш" |
Производство ферротитана из ильменита и рутила (с содержанием титана до 70%) алюмотермическим методом, без применения металлического титана. |
ДППТУ-3 |
г. Новосибирск, РФ |
"Новосибирский стрелочный завод - филиал ОАО "РЖД" |
Производство стали типа 110Г13Л, ХМЛ, 1Х18Н10Т, специальных и высокопрочных чугунов. |
ДППТУ-0,5АГ |
г. Воскресенск, РФ |
ООО "Южполиметалл-Р" |
Переплав аккумуляторного лома (свинца), переплав сплавов на основе меди |
ДППТУ-6 |
г. Аксу, республика Казахстан |
АО "Транснациональная Компания "Казхром" |
Производство ферросплавов, переплав отсевов FeCr. |
ДППТУ-6 АГ |
г. Сухой Лог, Свердловская обл. |
ОАО "Сухоложский завод вторичных цветных металлов" |
Переработка шлаковых отходов алюминиевых производств и отходов алюминиевых сплавов, включая стружку. |
ДППТУ-1,5 |
г. Санкт-Петербург |
ОАО ГОЗ "Обуховский завод" |
Выплавка высоколегированных марок стали и сплавов |
ДМПТУ-12 (2шт.) |
Н.Новгород, РФ |
ОАО "ГАЗ" |
Миксеры для нагрева, выдержки и доводки чугуна, выплавляемого в вагранках, могут быть применены для получения стали, сплавов на основе алюминия и меди. Обладают возможностью ведения активных металлургических процессов. |
Сертификат соответствия № РОСС RU.ТЧ02.ВО1918. Разрешение № РРС 00-21598
Результаты промышленной эксплуатации ДППТУ-НП широко опубликованы и представлены на сайте ООО «НТФ «ЭКТА»
На ДППТУ-НП освоена выплавка любых марок сталей: от Ст.3, Ст.40, ХМЛ, 5ХНМ, 4Х5МФС, 110Г13Л, Р5М5, Р18, нержавеющих хромоникелевых сталей, типа 10Х17Н13М3Т, 06Х20Н14С2, азотосодержащих типа 03Х17Г17ДАМБ; безникелевых нержавеющих сталей; штамповых сталей, типа 4Х5Р2ФС; высокохромистых сталей типа 95Х18, специальных сталей и сплавов, типа 14Х20Н25В5МБ-П и других аналогичных; серых чугунов марок от СЧ15 до СЧ30 с возрастанием марки от П45, Ф55 до П в СЧ30, высокопрочных чугунов ВЧ40 - ВЧ70 и других.
Сравнение показателей ДСП и ДППТУ-НП приведем на примере работы 20-тонной дуговой печи переменного тока ДСП-20 до и после ее реконструкции по методике ООО "НТФ "ЭКТА" в ДППТУ-20, на заводе "Тяжпрессмаш" (г. Рязань), таблицы 2 и 3.
Вместимость печи 22-30 тонн, по условиям электроснабжения мощность ДППТУ-НП увеличена только с 8,5 МВА до 10,79 МВА, т.е. печь «медленная». На печи установлен водо-охлаждаемый свод, используются классические технологии, в том числе - рудный кип.
Табл.2
Сравнение показателей работы ДСП-20 до реконструкции и после ее реконструкции в универсальную дуговую печь постоянного тока нового поколения - ДППТУ-20 на заводе «Тяжпрессмаш»
№№ п/п |
Наименование показателей |
ДСВ-20 (переменный ток) |
ДППТУ-20 (постоянный ток) |
1 |
2 |
3 |
4 |
1. |
Пыль, мг/м3 |
27,2 |
9,9 |
2. |
Шум, дБА |
98 |
84 |
3. |
Расход электроэнергии, кВт·ч/т жидкой стали |
890 |
710 |
4. |
Производительность по жидкому металлу, т/ч |
4,54 |
7,16 |
5. |
Средняя длительность плавки, ч |
4,92 |
3,0 |
6. |
Угар металла общий, % |
5 |
3 |
7. |
Расход электродов, кг/т жидкой стали |
14,0 |
2,12 |
8. |
Расход FeSi, кг/т жидкой стали |
13,8 |
11,2 |
9. |
Расход FeMn, кг/т жидкой стали |
6,3 |
5,1 |
10. |
Расход FeCr, кг/т инструментальной жидкой стали |
14,6 |
12,0 |
11. |
Расход FeV, кг/т инструментальной жидкой стали |
2,4 |
1,1 |
12. |
Расход FeMo, кг/т инструментальной жидкой стали |
2,1 |
2,1 |
13. |
Расход извести, кг/т жидкой стали |
48,0 |
20,7 |
14. |
Расход шамота, кг/т жидкой стали |
12,1 |
2,7 |
15. |
Расход раскислительной смеси (известь, FeSi 45, кокс), кг/т инструментальной жидкой стали |
78,22 |
46, 18 |
Табл.3
Улучшение показателей качества - уровень повышения соответствия ГОСТ, в %.
(за 0 - до реконструкции)
По химическому составу |
0 |
35 |
Предел текучести |
0 |
90 |
Предел прочности на разрыв |
0 |
60 |
Относительное удлинение |
0 |
45 |
Ударная вязкость |
0 |
80 |
Улучшение по УЗК валов (SEP1921) |
0 |
45 |
Однородность химического состава и температуры расплава, уменьшение неметаллических включений значительно увеличивают степень переохлаждения при кристаллизации и, как следствие, создают благоприятные условия для улучшения структуры металла. Это подтверждается данными центра управления качеством и независимой экспертизой Франции. Отклонения по химсоставу снизились на 35 %, уровень механических свойств на сталях для отливок и кузнечных слитков на 5-20 %, уровень несоответствия ГОСТ снизился на 90 %, соответствие ультразвукового контроля повысилось в поковках на 15 %, экспортных валах - на 45 %. На «старой» и «новой» печах количество плавок с содержанием фосфора более 0,035 % - 18 % и 2 % соответственно; с содержанием серы более 0,025 % - 33 % и 15 %. Аналогичные изменения наблюдаются со средними значениями этих элементов.
Ниже приведены исследования макро и микроструктуры материала заготовок валов, проведенных Центральной лабораторией ОАО «Тяжпрессмаш».
Исследованием установлено. Плавка ст.35 Ø 300: макроструктура: точечная неоднородность балл 1 ГОСТ 10243-75; микроструктура: перлит + феррит, величина зерна балл 6, ГОСТ 5699-82. Плавка ст. 35 Ø 380: макроструктура: точечная неоднородность балл 1, ГОСТ 10243-75; микроструктура: перлит + феррит, величина зерна балл 7, ГОСТ 5639-82. Плавка ст. 45 Ø 400: макроструктура: точечная неоднородность балл 1, ГОСТ 10243-75; микроструктура: перлит+феррит, величина зерна балл 7, ГОСТ 5639-82. Плавка ст. 35 Ø 410: макроструктура: точечная неоднородность балл 1, ГОСТ 10243-75; микроструктура: перлит + феррит, величина зерна балл 6, ГОСТ 5635-82.
При выплавке изделий данного типа на печи до и после реконструкции получены следующие результаты.
Было: точечная неоднородность 3-4 балл, ликвационные зоны, рыхлота осевая, неметаллические включения в виде скоплений, микроструктура 4-5 балл.
Стало: точечная неоднородность - 1 балл, ликваций - нет, рыхлот - нет, неметаллические включения - разрозненные, не выше 1,5 балл, стабильная микроструктура 6-7 балл.
По результатам анализа центральной заводской лаборатории плавок на ДСВ-20 и печи, реконструированной на ДППТУ-20, получены следующие результаты: - отклонения по химическому составу снизились на 35 %; - соответствия механических свойств литой стали увеличились на 35 %; - соответствие требованиям УЗД на всех подвергнутых проверке поковках увеличилось на 15 %, экспортных валов на 45 %; - возросла стабильность результатов механических испытаний: разброс снизился на 20 %, сходимость увеличилась на 40 %; - возрос уровень механических свойств на сталях: 1) 25Л; σв - на 5 %; δ - на 7 %; αк - на 10 %; 2) 35Л; σт - на 9 %; σв - на 10 %; δ - на 7 %; αк - на 15 %; 3) 45Л; σт - на 18 %; σв - на 15 %; δ - на 11 %; ψ - на 12 %; 4) 20ГСЛ; σт - на 5 %; σв - на 12; 5) 35 ХМЛ; σв - на 14 %; 6) Ст 20; σт - на 8 %; σв - на 4 %; δ - на 6 %; ψ - на 9 %; 7) 40ХМА; σт - на 9 %; σв - на 13 %; δ - на 20 %; αк - на 20 %; 8) 40ХН2МА; σт - на 11 %; σв - на 6 %; δ - на 8 %; ψ - на 4 %; αк - на 11 %.
Несоответствия поковок и отливок по механическим свойствам снились: предел текучести - на 90 %, предел точности - на 60 %, относительное удлинение - на 45 %, относительное сужение - без изменений, ударная вязкость - на 80 %.
Высокие показатели качества достигнуты за счет сохранения принципа «варить» сталь в печи ДППТУ-НП, а не синтезировать сталь в установке печь-ковш.
Годовой экономический эффект от перевода печи ДСП в ДППТУ-НП составил около 52 млн. руб., по отдельным маркам стали экономия на 1 т жидкого металла составила 3600 руб. Срок окупаемости - 10 месяцев!
Основными экономообразующими статьями стали: замена науглероживателя чугуна передельного на стальной лом и графитированную стружку ~ 12 млн. руб., на разделке шихты ~ 13 млн. руб., от снижения расхода ферросплавов ~ 3 млн. руб., электроэнергии 2,2 млн. руб.
Структура полученного экономического эффекта отражает и подтверждает то, что экономия электроэнергии не может быть главной целью реконструкции. Основой технико-экономических показателей являются стоимость сырья и материалов. Из анализа показателей следует, что установка дуговых печей нового поколения, с целью повышения производительности и качества оправдана и быстро окупает себя. В данный расчет не включена экономия затрат на экологию, которая также является одной из весомых экономических составляющих.
Уникальные возможности ДППТУ-НП подтверждены освоенными в них уникальными технологиями, многие из которых, как ранее считалось, вести в дуговых печах невозможно.
Так, например, серийно производится сплав на основе алюминия -АК7ч, который соответствует химическому составу и превосходит по механическим свойствам ГОСТ 1583-93. В литом термообработанном состоянии на отлитых в металлическую форму образцах предел прочности - не менее 216 МПа, относительное удлинение - не менее 2 %, твердость по Бринеллю - не менее 94,9 ВА, при этом содержание кремния колеблется от 6,15 до 7,15 %, магния от 0,25 до 0,4 %, железа от 0,1 до 0,3 % структура отличается повышенной дисперсностью неметаллических включений. Содержание водорода - 0,1-0,2 см3/100г металла, а пористость отливок всегда соответствует 1 баллу шкалы пористости по ГОСТ 1589-93.
ДППТУ-НП является единственным агрегатом, в котором, в процессе расплавления сплавов на основе алюминия, идет интенсивное удаление водорода и неметаллических включений. Быстрое расплавление позволяет при переплаве алюминия, имеющего стальные приделки получать расплав без насыщения железом. Переплав, всегда сопровождается получением пористости соответствую-щей 1 баллу шкалы пористости по ГОСТ 1589-93, а содержание водорода, как правило 0,1-0,2 см3/100 г металла, в литом состоянии ряда сплавов может достигать максимум 0,4 см3/100 г. Это по-зволяет при гораздо меньших затратах выходить на качественное литье при переработке вторичного алюминии. За счет исключения множества технологических операций, повышения качества сплавов, себестоимость технологического передела снижается: в 5 раз в сравнении с переделом в индукци-онных печах и в 15 раз в сравнении с газовыми печами.
Для новых и реконструируемых предприятий НТФ «ЭКТА» предлагает Заказчикам сертифицированный ряд плавильных печей и миксеров.
Список литературы
1. В.С. Малиновский, М.К. Закомаркин, М.М. Липовецкий, Н.А. Пономарев и др. «Требования к конструкции дуговой сталеплавильной печи постоянного тока». Металлургическая и горнорудная промышленность, №4, 1988 г.
2. М.К. Закомаркин, М.М. Липовецкий, В.С. Малиновский «Дуговая сталеплавильная печь постоянного тока емкостью 25 т на ПО «Ижсталь». Сталь, № 4, 1991 г. - С. 31-34.
3. Патент № 2104450 РФ. С 22 В 9/21. «Способ электроплавки и дуговая печь для его осуществления» Малиновский В.С., 04.01.1995 г.
4. Патент № 2048662 РФ. С 22 В 9/20. «Способ электроплавки и дуговая печь для его осуществления». Малиновский В.С., Чудновский А.Ю., Липовецкий М.М., 31.03.1992 г.
5. Патент № 2112187 РФ. Н 05 В 7/06. «Подовый электрод электропечи» Малиновский В.С., 13.03.1996 г.