НОВОЕ ПОКОЛЕНИЕ ДУГОВЫХ ПЕЧЕЙ ПОСТОЯННОГО ТОКА ДЛЯ МЕТАЛЛУРГИЧЕСКОГО И ЛИТЕЙНОГО ПРОИЗВОДСТВ
к.т.н. В.С. Малиновский («НТФ «ЭКТА»),
к.т.н. Л.В. Ярных («НТФ «ЭКТА»)
д.т.н., проф., А.В. Афонаскин (ОАО «Курганмашзавод»)
В последнее время в мире широкое распространение получили сверхмощные дуговые печи переменного и постоянного тока. Эти печи поставляют ведущие западные фирмы «Манесман», «Даниэли», «Фест-Альпине» и др., те же технические решения используют отечественные специалисты при реконструкции дуговых сталеплавильных печей переменного тока (ДСП).
Основой новых печей является совмещение дугового нагрева с нагревом источниками тепла от сгорания газа, мазута, угольной пыли, растворенного в металле углерода и самого металла. Это совмещение объясняется необходимостью экономии электроэнергии и резкого увеличения емкости и производительности печей, экономией графитированных электродов. Результатом реализации этой концепции явились вынужденный отказ от всех технологических процессов, ранее проводимых в ДСП, и их перенос в установку печь-ковш. В современной сверхмощной ДСП проводится форсированное расплавление металла и совмещенный с ним окислительный процесс. Другие технологические операции в печи провести нельзя и они проводятся в процессе внепечной обработки. Поскольку технологические процессы и результаты их ведения зависят не от дугового нагрева, а от экзотермических реакций, и за их счет поступает основное тепло для плавления металла сверхмощные печи трудно назвать дуговыми, а пути их совершенствования – совершенствованием ДСП. Если проводить оценку энергетического вклада источников тепла, то правильнее было бы созданные печи называть, может быть, мартено-конверторными с дуговым подогревом, рис.1. Приведенная на рис.1. информация является по EOF и СДП усредненной и получена в результате обработки рекламных данных зарубежных печей. При рассмотрении специалистами данной информации по отношению к своим предприятиям, сохраняя методику анализа, можно уточнить показатели с учетом своих условий и показателей предлагаемого печного оборудования. Но для печей, использующих тепло экзотермических реакций, есть свой путь развития без дугового нагрева, воплощенный, например, в энергетически оптимизированных печах (EOF). Созданные сверхмощные печи, если их сравнивать с ДСП, усилили недостатки последних – значительно с 3-4,5 % до 8,5-12,0 % возрос угар шихты, многократно выросли пылегазовыбросы и аккумулированное в них тепло, а в газовыбросах серьезно возросло количество вредных компонентов и СО2, резко возросли отходы в виде шлаков, потерялась возможность сохранять легирующие элементы в шихте, что вызывает значительное увеличение расхода ферросплавов, печи вынужденно работают с «болотом».
Рис.1. Сравнение удельной электрической энергии и тепла экзотермических реакций в сталеплавильных печах.
Снижение вклада энергии, поступающей в металл от электрических дуг, до уровня 25-40 % от подведенной мощности послужило одной из причин отсутствия заметных различий в использовании дуг постоянного и переменного тока и, поэтому, в сверхмощных дуговых печах постоянного и переменного тока реализуются примерно одинаковые параметры, свойственные комбинированным печам, которые используются в нашем докладе с обобщенным названием сверхмощная дуговая печь (СДП). [1, 2, 3]
Концепцией нашей работы является развитие и совершенствование дугового нагрева без привлечения других источников тепла, сохранение и совершенствование технологий ДСП в чистом виде. Этапами развития были создание плазменных плавильных печей постоянного тока (ПСП) [4], создание технологических процессов на их основе, принципиальное упрощение плазменных печей с сохранением их технологических возможностей [5, 6], расширение технологических возможностей печей путем введения новых электрических режимов плавления, нового способа МГД перемешивания, изменения нагрузочных характеристик, а в ряде случаев, конструкции графитированных электродов, разработки новых подовых электродов и методов, обеспечивающих их надежную, длительную и безопасную работу, разработки специализированных источников электропитания и систем управления процессом плавки [7, 8, 9]. Комплексное решение проблем позволило нам создать новый тип печей – дуговые печи постоянного тока нового поколения (ДППТНП). Объем доклада не позволяет нам описать их особенности. Они изложены в [2-12].
В данном докладе приведены технологические и технико-экономические результаты промышленной эксплуатации ДППТНП, некоторые сравнения с СДП, обоснована целесообразность применения ДППТНП в металлургической промышленности.
Из всех изложенных ниже материалов ясно следует, что проводимые зарубежными и отечественными специалистами сравнения дуговых печей постоянного и переменного тока не имеют никакого отношения к ДППТНП, разработанных специалистами НТФ «ЭКТА» в содружестве с ведущими предприятиями России.
Мы также хотим обосновать свое мнение о том, что выбранный на сегодняшний день метод производства стали в СДП в определенной мере тупиковый с точки зрения энергоресурсосбережения, экологии, повышения качества металла, снижения его себестоимости.
Технологические возможности ДППТНП.
В ДППТНП освоен промышленный выпуск низко и высоколегированных сталей, например, инструментальных сталей - Р6М5, Р18; нержавеющих хромоникелевых сталей – 12Х18Н9Т, 12Х18Н10Т, 08Х18Н10Т, 08Х18Н10, 17Х18Н9, 10Х17Н13М2Т (ЭИ448), 10Х17Н13М3Т (ЭИ432), 12Х20Н14С2, 06Х20Н14С2, СВ–04Х19Н9, СВ–06Х19Н9Т, СВ-08Х21Н10Г6; азотосодержащих сталей – 03Х20Н16АГ6, 07Х13АГ20 (4С46), 03Х13АГ19 (4С36), 07Х13Н4АГ20 (4C52), 03Х19АГ3Н10, 06Х18Г9Н5АБ (4С51), 03Х19Н1516М2АВ2 (4С39), 05Х15Н916АМ (4С31), 06Х17Г15КАН (А43), 06Х17Г17ДАМБ (А9У); безникелевых нержавеющих сталей, штамповых сталей – 3Х3М3Ф, 35Х3МЭФС, 4Х5Р2ФС (ЭИ958), 4Х2В5МФ (ЭИ959), 4ХВМФС (ДИ22); высокохромистых сталей – Х12, Х12М1, Х12МФ, Х12ВМ, 95Х18; литейных сталей 25Л-50Л, 35ХНЛ, 30ХМЛ, 28СГТЛ, 40ХЛ, 110Г13Л, 20Х13Л, Ст.3, Ст.20, Ст.40 и др.; сплавов на никелевой основе типа ЭП742ЭП, 50Н, 47НД; специальных сталей и сплавов типа 14Х20Н25В5МБ-П, ХН68ВМТСК (ЭП693) и других аналогичных; серых чугунов марок от СЧ15 до СЧ30 с возрастанием марки от П45, Ф55 до П в СЧ30; ВЧ40 – ВЧ70 и др.; сплавов на основе алюминия АЛ9, АК7ч, АК12, АК18 и лигатур на основе алюминия; сплавов на основе меди.
2. Угар металла.
Угар металла, по сравнению с ДСП, применяемых в специальной электрометаллургии и литейном машиностроении, многократно снижен и не превышает 0,75 – 1,5 %, угар ферросплавов снижен на 85-95 %, за счет чего слив металла с каждой тонны шихты увеличен на 40-60 кг [6, 10].
Особенности плавления в ДППТ-25 и разработанная технология выплавки быстрорежущей стали позволили не только существенно увеличить усвоение легирующих элементов и снизить потери металла (табл. 1), но и на 1,5 – 3,0 кг/т уменьшить расходы порошков алюминия, силикокальция, ферросилиция. Сравнительные показатели выплавки быстрорежущих марок стали в ДСП-25 и ДППТ-25 приведены в табл.1.
Сравнительные показатели выплавки быстрорежущих марок стали*
Таблица 1.
ПОКАЗАТЕЛИ |
ДППТ-25 |
ДСП-25 |
Усвоение легирующих элементов (марка Р6М5), %: хром
ванадий
вольфрам
молибден |
97,9
95,8
97,4
94,8 |
94,6
88,3
93,9
92,4 |
Сквозной угар, % |
2,49 |
9,57 |
**Расходный коэффициент, кг/т по стали марки: Р6М5
Р18
Р6М5К5 |
1056 (235)
1063 (21)
1053 (50) |
1108 (196)
1110 (40)
1110 (26) |
*По данным балансовых плавок
**Статистические данные технического отчета, в скобках – количество плавок.
При переплаве неподготовленной чугунной стружки на агрегате ДППТ-3АГ, специализированном для ведения данного процесса, получены следующие показатели (табл.2).
Таблица 2.
Наименование показателей |
Требования стандартов, ТУ*, % |
Фактические показатели, % |
С |
3,10-3,30 |
3,63±0,08 |
Si |
1,80-2,00 |
2,28±0,13 |
Mn |
0,30-0,80 |
0,40±0,04 |
S |
0,05 |
0,007±0,004 |
* Превышение фактического содержания элементов требований ТУ (состав исходного материала) вызвано отклонениями химсостава исходного материала от ТУ.
Возможность переплава чугунной стружки с сохранением всех элементов и глубокой десульфурацией в других типах печей нам неизвестна.
При выплавке марганцовистой стали 110Г13Л в печном агрегате ДППТ-6АГ ОАО «Курганмашзавода» по сравнению с выплавкой в печи ДСП-5МТ угар металла уменьшился с 6,0-6,5 % до 0,5-1,0 %. Это дает 50-60 кг/т дополнительного металла и экономию марганца 11,6 кг/т (анализ 240 плавок).
Расход графитированных электродов, допускаемые плотности токов.
На ДППТНП используются, в зависимости от требований технологии, два вида графитированных электродов и электродных узлов:
- обычные электроды, применяемые на ДСП, удельный расход электродов – 1,3-1,5 кг/т.
- графитированные электроды обычной конструкции, закрепляемые на медной водоохлаждаемой штанге – 0,8 кг/т.
- графитированные электроды с центральным отверстием для подачи аргона, азота – 0,4 кг/т, при подаче кислородно-аргоновой смеси – 0,6 кг/т.
Конструкции электродов с водоохлаждаемой штангой нельзя использовать на дуговых печах постоянного и переменного тока без специальных режимов плавления, применяемых на ДППТНП. В ДППТНП, разработанная нами система плавки предотвращает разрушение электрододержателей «паразитными» дугами и обеспечивает работу обычных графитированных электродов при плотности тока 60-80 А/см2. Это позволяет не разрабатывать специальные электроды для крупнотоннажных печей, т.к. стандартный электрод диаметром 610 мм в ДППТНП допускает токовую нагрузку до 200 кА, достаточную для работы печей емкостью до 130 т.
Другой особенностью ДППТНП является практическое отсутствие науглероживания металла от электродов. Так при выплавке стали 04Х19Н9 и последующей выдержке расплава в печи в течение 6 часов науглероживание составило 0,005 %, т.е. на уровне погрешности анализа.
Экология.
Рассматриваются следующие элементы воздействия печей на окружающую среду: газовые выбросы, шум, шлакообразование.
Газовые выбросы. Технологии плавки в ДППТНП проводятся без использования газокислородных горелок, вспенивания шлака и подачи кислорода (кроме в технологически обоснованных процессах), угольных порошков, мазута и т.д. и практическом отсутствии прокачки воздуха через печное пространство, обеспеченное высоким уровнем стабилизации электрического режима [6, 7, 8,10]. При выплавке углеродистых сталей в составе печной атмосферы присутствуют 35-50 % СО; 8,2-9,4 % CO2; 0,4 % О2; 0,0003 % SO2; 0,002-0,0003 % NO и N2 остальное [13]. При выходе из печи СО догорает до СО2 и его содержание снижается до 0,5-0,8 %. Наличие диоксинов, фуранов, цианидов, фторидов отмечено не было. При наличии в шихте органических включений, масла, влаги в начальный период плавки образуются продукты их возгонки, которые при выходе из печи догорают до завершенных оксидов. Для сравнения с ДППТНП приведем показанные в работе [14] токсичные примеси в газах ДСП (табл.3)
Таблица 3.
Компоненты |
Средняя концентрация, мг/м3 |
Удельные выбросы, г/т |
Окись углерода |
13500,0 |
1350,0 |
Окиси азота |
550,0 |
270,0 |
Оксиды серы |
5,0 |
1,6 |
Цианиды |
60,0 |
28,4 |
Фториды |
1,2 |
0,56 |
ДСП необходимо оснащать мощными системами отсоса газа непосредственно из печи, производительность которых должна быть выше производительности естественной прокачки газа через печь, вызванной колебаниями электрического режима [5]. В ДППТНП в систему вентиляции забираются газы, выходящие из печи самопроизвольно. Это позволяет не менее чем на порядок снизить производительность системы вентиляции. Применение комбинированных ДСП или СДП с использованием газокислородных горелок, энергетического кислорода, вспенивания шлака требует многократного увеличения производительности систем газоудаления даже в сравнении со «старыми» ДСП и увеличивает количество и расширяет состав токсичных примесей в газовых выбросах. Резкое возрастание образования СО2 может неоправданно создать проблемы, связанные с Киотским соглашением. Значительно возрастает количество воздуха, прокачиваемого через печь, и связанный с этим дополнительный угар металла и образование NO.
Пылевыбросы. Исследования пылегазовыбросов из ДППТНП проводились на печах различной емкости и их результаты изложены в [13]. Из них следует, что удельные выбросы пыли из ДППТНП составляют 0,97 кг/т, в ДСП – 7,47 кг/т, в СДП – 35 кг/т. Это дало нам основание не оснащать ДППТ-25 ПО «Ижсталь» и ДППТНП-6АГ ОАО «Курганмашзавод» системами пылегазоочистки. Проведенные замеры пылегазовыбросов сложной в экологическом отношении стали 110Г13Л показали, что выброс пыли из ДППТ составил 0,7914 г/с при ПДВ – 0,98 г/с, в т.ч. Mn – 0,0266 г/с при ПДВ – 0,1486 г/с. Интенсивное МГД перемешивание металла в ДППТНП обеспечивает однородность температуры и химсостава во всем его объеме. Это обеспечивает при интенсивном рудном кипе, например, стали ХМЛ отсутствие заметных пылегазовыбросов и нормы ПДВ не превышаются [10]. Можно утверждать, что при реконструкции заводов с мартеновскими печами удается ограничиться их системами газоотвода, не создавая системы пылегазоочистки. На рис.2 приведена оценка сравнительных удельных выбросов газов из печных труб печей ДСП, СДП, ДППТНП, демонстрирующая принципиальные преимущества ДППТНП.
Рис.2. Сравнение удельных объемов пылегазовыбросов из печных труб дуговых печей
Шум. Измерения уровня звука в дБА в ДППТ-12 и ДППТ-25 и ДСП12 и ДСП25 выявили уровни 92, 92 и 100 и 108 соответственно. Уровень звука в СДП превышает 115 дБА в основном за счет работы газовых горелок.
Шлакообразование. Оно очевидно и является следствием угара шихты, который в ДППТНП - 1,5 %, в ДСП – 4,5 %, в СДП – 8,5-12,0 %, где к тому же шлакообразующие материалы дополнительно подают для организации вспенивания шлака. В ДППТНП за счет малого окисления шихты первичный шлак практически не образуется. Это позволяет формировать шлак с заданными свойствами во все периоды плавки и при интенсивном МГД перемешивании расплава вести его глубокую десульфурацию и дефосфорацию при пониженном расходе шлакообразующих элементов.
Например, разработанная технология выплавки быстрорежущей стали в ДППТ-25 обеспечила получение хорошо раскисленного высокоосновного шлака с минимальным содержанием оксидов легирующих элементов. Среднее по 3 балансовым плавкам содержание оксида хрома снизилось с 6,7 % перед раскислением шлака периода плавления до 1,3 % перед выпуском плавки, оксида вольфрама – с 3,1 до 0,3 %, оксида ванадия – с 3,1 до 0,1 %, основность шлака, выраженная отношением оксидов кальция и кремния, в те же моменты плавки составила 0,6 и 2,5 соответственно.
Энергосбережение.
Источником тепла в ДППТНП является электрическая дуга. Тепло экзотермических реакций при низком угаре шихты незначительно и его вкладом можно пренебречь. На ОАО "Курганмашзавод" при выплавке стали 110Г13Л достигнут расход электроэнергии на плавку 390 кВт·ч/т, усредненный удельный расход электроэнергии за месяц двухсменной работы с длительными технологическими простоями выявляет расход электроэнергии 550 кВт·ч/т, в подряд идущих плавках 450 кВт·ч/т (полный металлургический цикл). На крупнотоннажных печах или печах, работающих в три смены, мы можем надеяться на то, что удельный расход электроэнергии не превысит 420 кВт·ч/т. На ОАО "Курганмашзавод" в среднем удельный расход электроэнергии по сравнению с ДСП снизился на 15-20 % при примерно равной мощности источников электропитания и значительном росте производительности печи.
На рис.3 приведены сравнительные диаграммы расходов энергоресурсов на ДСП, СДП и ДППТНП, приведенные через их стоимость к удельным расходам электроэнергии. При этом мы учли не только приводимые в рекламных источниках данные по экономии электроэнергии, но и приведенные к стоимости электроэнергии другие источники тепла – газ, кислород, сгоревшую шихту, затраты электроэнергии в системах пылегазоочистки, в печах-ковшах, без которых эксплуатировать эти печи нельзя. Сравнение очевидным образом выявляет сверхрентабельность ДППТНП и это становится еще более существенным, если учесть экономию ферросплавов за счет сохранения легирующих элементов шихты в ДППТНП. Цены на материальные и энергоресурсы взяты по данным «Даниэль». Каждому Заказчику легко пересчитать таблицу с учетом своих цен и параметров предлагаемых печей, включая потери легирующих элементов шихты.
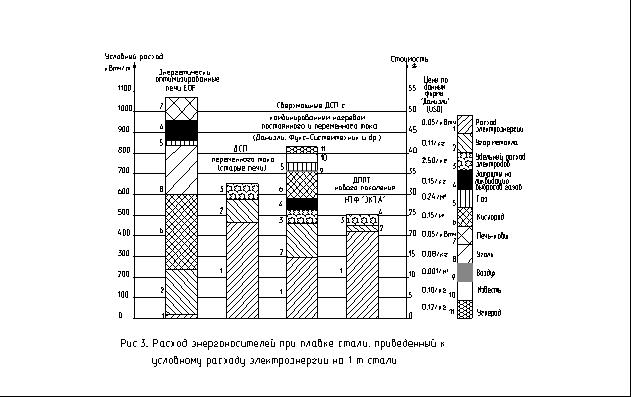
Большой проблемой современных печей является мощный вынос с газом избыточного тепла, которое вызывается крайне неэкономичным использованием энергоносителей. Если посчитать все выделяемое тепло в печи, учитывая тепло экзотермических реакций при сгорании 8,5-12 % шихты, то условный удельный расход энергии достигает 1000 кВт·ч на тонну расплавляемого металла и значительная часть этой энергии, запасенной в отходящих из печи газах, должна быть рассеяна перед подачей газа на фильтры пылеочистки. В ДППТНП доля тепла, отводимого отходящими газами не превышает 0,3-0,7 % подведенной мощности и проблемы с утилизацией тепла отсутствуют.
Качество металла.
Выше было показано множество марок сталей и сплавов, выплавка которых освоена в ДППТНП и их прототипах ПСП, качество которых полностью соответствует ТУ и ГОСТ. Многие из этих металлов нельзя выплавить в ДСП и их производят в вакуумно-индукционных печах (ВИП), а некоторые можно сварить только в ДППТНП.
Основными мероприятиями, позволившими усовершенствовать технологические процессы в ДППТНП по сравнению с ДСП и ПСП, явились введение двух-трехступенчатого по току и напряжению режима плавления, нового типа МГД перемешивания расплава, замена вольфрамовых катодов на графитированные электроды с низкой эрозией, исключение для большинства, в т.ч. высоколегированных марок, стали и сплавов применения аргона, разработки более совершенных и надежных подовых электродов. Это позволило решить ряд важнейших вопросов: практически устранить угар шихты и ферросплавов, работать с контролируемыми составами атмосферы печи и шлака во все периоды плавки, резко увеличить эффективную поверхность взаимодействия металла и шлака, ускорить ведение процессов расплавления шихты и технологических, устранить локальные перегревы металла под дугой, обеспечить равномерность температуры и химсостава во всем объеме расплава, глубокое удаление и диспергирование оставшихся в металле неметаллических включений, интенсивную, в отличие от ДСП и ПСП, дегазацию расплава, управляемое воздействие на наследственную структуру металла. Данные возможности ДППТНП позволили на внедривших их предприятиях получить рост качества практически недостижимый на других типах печей.
Сравним влияние переплава на качество в ДППТНП и ДСП на примере стали 110Г13Л, производство которой ведет ОАО "Курганмашзавод".
Были проведены сравнительные испытания стали 110Г13Л ГОСТ 977-88, выплавленной в печи ДС-5МТ (плавки 1 и 2) и в печи ДППТ-5АГ (плавки 3 и 4) на изгиб, твердость и микроструктуру.
Результаты испытаний приведены в таблицах 4, 5, 6.
Химсостав стали 110Г13Л.
Таблица 4
№ плавки |
С |
Mn |
Si |
S |
P |
Cr |
Ni |
1 ДС |
1,36 |
12,08 |
0,62 |
0,005 |
0,060 |
0,54 |
0,22 |
2 ДС |
1,38 |
11,81 |
0,55 |
0,002 |
0,060 |
0,61 |
0,22 |
3 ДППТ |
1,35 |
12,46 |
0,65 |
0,002 |
0,057 |
0,47 |
0,25 |
4 ДППТ |
1,36 |
11,99 |
0,73 |
0,003 |
0,053 |
0,42 |
0,27 |
Механические свойства
Таблица 5
Номер плавки |
Стрела прогиба, мм |
Твердость, НВ |
1 ДС |
2,8 |
255 |
2 ДС |
2,5 |
269 |
3 ДППТ |
3,6 |
269 |
4 ДППТ |
4,4 |
269 |
Условия испытания на изгиб при постоянной нагрузке 6 т, расстояние между опорами 200 мм.
Результаты металлографического исследования*
Таблица 6
Номер плавки |
Балл аустенитного зерна |
Балл по карбидам |
1 ДС |
2 |
2а |
2 ДС |
2-3 |
2а |
3 ДППТ |
1 |
2а |
4 ДППТ |
1 |
2а |
* Оценка произведена по шкале контроля микроструктуры траков после закалки.
Испытания траков, изготовленных из стали 110Г13Л, в реальных условиях выявили в разы увеличенную износостойкость.
При плавках на ДППТ-5АГ из-за низкого угара металла практически не образуется первичный шлак, что позволяет формировать шлак высокого качества, который в условиях интенсивного перемешивания активно взаимодействует с металлом. За счет ускорения ведения технологических процессов на печи достигнуто так же сокращение времени выплавки углеродистых сталей со 150 до 60 мин. при значительном улучшении их качества.
В ряде производимых на ОАО «Курганмашзавод» находятся стали типа ХМЛ и хладостойкая сталь 30ХМЛ. Первая, предназначенная для производства литой заготовки для запорной арматуры. В мире литая заготовка выпускается на давление до 150 атм., на ОАО «Курганмашзавод» освоено производство литой заготовки на давление 750 атм. Основой повышения механических свойств явилось широкое использование различных комбинаций модификаторов и плавка в ДППТНП. Подробнее свойство, а в особенности содержание растворенных газов – азота и водорода исследовалось в стали 30ХМЛ.
Образцы для испытаний изготавливались из клиновых проб. Все исследуемые плавки были предварительно раскислены алюминием в количестве 0,1 % по массе. Состав и количество использованных модификаторов приведены в табл.7.
Варианты модифицирования
Таблица 7
№
образца |
Количество добавок модификаторов, вес.% |
СК25 |
ФС30РЗМ30 |
ФСМг7 |
1 |
0,20 |
- |
- |
2 |
- |
0,10 |
- |
3 |
- |
0,15 |
- |
4 |
0,10 |
0,20 |
- |
5 |
0,20 |
0,10 |
0,10 |
6 |
0,20 |
0,10 |
0,20 |
Химический состав образцов приведен в табл.8.
Содержание химических элементов в образцах из клиновых проб, %
Таблица 8
№ обр. |
C |
Mn |
Si |
S |
P |
Cr |
Ni |
Mo |
Cu |
Al |
1 |
0.26 |
0.41 |
0.44 |
0.024 |
0.031 |
0.83 |
0.15 |
0.22 |
0.11 |
0.065 |
2 |
0.25 |
0.38 |
0.32 |
0.039 |
0.031 |
1.00 |
0.17 |
0.21 |
0.17 |
0.047 |
3 |
0.25 |
0.37 |
0.31 |
0.040 |
0.032 |
1.02 |
0.16 |
0.21 |
0.14 |
0.079 |
4 |
0.31 |
0.57 |
0.46 |
0.033 |
0.032 |
1.24 |
0.14 |
0.21 |
0.13 |
<0.01 |
5 |
0.32 |
0.76 |
0.53 |
0.028 |
0.025 |
0.92 |
0.11 |
0.22 |
0.12 |
0.055 |
6 |
0.33 |
0.74 |
0.58 |
0.027 |
0.024 |
0.91 |
0.11 |
0.21 |
0.12 |
0.058 |
Результаты анализа содержания водорода и азота в образцах приведены в табл.9.
Содержание газов в образцах, в %
Таблица 9
№ образца |
Азот |
Водород |
2 |
0,0145 |
0,00032 |
3 |
0,0125 |
0,00031 |
4 |
0,0150 |
0,00030 |
5 |
0,0090 |
0,00028 |
6 |
0,0011 |
0,00024 |
Эти результаты позволили добиться предельно высоких механических характеристик металла, ударная вязкость равна 1,0-1,4 МДж/м2 вместо 0,6-0,7 МДж/м2 после переплава в ДСП (в термообработанном состоянии).
На ОАО "Курганмашзавод" в электродуговых печах ДС-5МТ выплавлялись серые чугуны различных марок от СЧ15 до СЧ30 включительно и ВЧ40-ВЧ70.
Содержание перлита в СЧ30 возрастает с возрастанием марки от П45, Ф55 до П в СЧ30.
Плавка исходного чугуна для ВЧ осуществляется в дуговой печи с основной футеровкой.
С внедрением в производство дуговой печи, работающей на постоянном токе, процесс десульфурации значительно облегчился и ускорился за счет перемешивания металла и его активного взаимодействия со шлаком, основность которого составляет более 2,0.
В результате мы всегда имеем содержание серы в исходном чугуне не более 0,01 %, что позволяет уменьшить расход магниевой лигатуры до 1,0-1,2 %.
За счет глобулизации неметаллических включений в ЧШГ заметно возрастают механические и пластические свойства. Так чугун со следующим содержанием элементов: С=3,58; Si=2,13; Mn=0,68; S=0,007; Р=0,06; Cr=0,17; Ni=0,05 имеет предел прочности 60,6 кгс/мм2, а относительное удлинение 12,0 %.
Чугун следующего химического состава: С=3,23; Si=2,65; Mn=0,58; S=0,004; Р=0,06; Cr=0,17; Ni=0,06 имеет предел прочности 68,0 кгс/мм2, а относительное удлинение 8,4 %.
Следует отметить, что чугун выплавляли из рядовой шихты [10].
Таким образом, плавка исходного чугуна в дуговой печи постоянного тока за счет интенсивного перемешивания металла в процессе плавки и его активного взаимодействия со шлаком, позволяет значительно повысить пластичность ЧШГ при одновременном возрастании механических свойств, что подтвердило преимущество ДППТ перед другими видами нагрева при производстве чугуна.
Преимущества плавки в печи постоянного тока позволили предприятию повысить качество литых заготовок запорной арматуры для нефтегазового комплекса из конструкционных углеродистых и легированных сталей, отливок из чугуна.
При выплавке в ДППТНП сталей, сплавов, в т.ч. на основе алюминия, всегда реализуются результаты – измельчаются зерна кристаллов, снижаются количество неметаллических включений и растворенных газов, значительно возрастают механические свойства.
7. Электроснабжение.
Мощности источников питания дуговых печей переменного и постоянного тока соизмеримы и определяются требованиями по времени расплавления, наличием, отсутствием сторонних источников энергии.
Существенной отличительной особенностью источников питания дуговых печей постоянного тока является возможность их секционирования, что невозможно для печей переменного тока. Блочная схема источника питания облегчает условия транспорта, монтажа, холодного резерва при максимальном повышении надежности электроснабжения сверхмощных печей. По идеологии НТФ «ЭКТА» для ДППТНП емкостью 80-100 т целесообразно применение четырех блоков мощностью 20-25 МВА каждый для «быстрых» печей и 10-15 МВА для «медленных». При выходе из строя одного из блоков производительность печи может быть сохранена на уровне 80-90 % номинальной.
Применение блочных схем практически снимает многие проблемы внешнего электроснабжения. Создание любых по пульсности схем выпрямления обеспечивает естественное снижение гармонических составляющих тока во внешней сети. Выбор параметров источников питания, реализация соответствующих требований к системам управления и ведения режимов позволяет на 70-80 % устранить основной недостаток ДСП и СДП в части ударного и резко-переменного характера нагрузки.
Следствием выше изложенного является: возможность реконструкции действующих печей с увеличением их мощности без серьезного усиления системы электроснабжения, отказ в большинстве случаев от средств динамической компенсации, отказ либо применение нерегулируемых фильтрокомпенсирующих устройств ограниченной мощности.
Другой характерной особенностью построения источников питания ДППТНП является отказ от применения на печных трансформаторах ПБВ и РПН. При этом ступенчатое регулирование напряжения осуществляется по стороне выпрямленного тока за счет последовательно-параллельного соединения тиристорных мостов, что позволяет вести плавку при постоянной мощности и эффективно использовать установленную мощность трансформаторного оборудования [8, 11].
За последние годы разработано четвертое поколение источников питания ДППТНП, которые имеют малые габариты, высокую надежность и позволяют проводить реконструкцию действующих ДСП на существующих площадях.
При построении производства, например, с двумя «медленными» ДППТНП вместо одной СДП, способных передавать плавку на МНЛЗ каждые 40-45 минут, мощность источника ДППТНП будет выбрана в пределах 50-60 МВА. На СДП обычно устанавливают источник электропитания 80-110 МВА. Таким образом, суммарная мощность двух ДППТНП одного порядка с источником электропитания ДППТНП при полном цикле плавки в ДППТНП 80-90 минут. При работе ДППТНП в режимах только расплавления с окислением, «быстрая печь», т.е. с длительностью плавки от выпуска к выпуску ~35 минут, мощности источников питания ДППТНП и СДП одинаковы.
Производительность и емкость.
НТФ «ЭКТА» разрабатывает «быстрые» и «медленные» ДППТНП с соответствующими временами расплавления 30-35 минут и 50-60 минут. Организация процесса расплавления, МГД перемешивание расплава, обеспечивают расплавление шихты и нагрев расплава, высокую стойкость огнеупоров без использования кислорода, газокислородных горелок, вспенивания шлака, донных продувок, «болота». Поддерживая концепцию ДСП, предназначенных для ведения полного цикла плавки с проведением всех технологических периодов – окислительного, восстановительного, рафинировки мы обратили внимание на сокращение времени их ведения. Разработанная нами система МГД перемешивания расплава позволяет это делать. Так при рудном кипе, проводимом при выплавке стали ХМЛ на ДППТ-6АГ скорость обезуглероживания составила 0,1 % С за 3 минуты, время на формирование высокоосновного шлака – 2-3 минуты, расплавление легирующих элементов и выравнивание химсостава ванны расплава – 3-4 минуты. За счет этого время плавки на ДСП-5, составляющее 150 минут, было сокращено на ДППТ-6АГ до 50-60 минут при времени расплавления – 35-40 минут. Следует отметить то, что новые параметры плавки были достигнуты на печах с примерно равными мощностями источников питания – ДСП-5МТ – 4МВА, мощность тиристорного преобразователя печи ДППТ-6АГ – 4,2 МВА. Эти темпы возможно сохранить для печей емкостью до 100 тонн. Если на ДППТНП делать полупродукт, ограничиваясь окислительным периодом, как это делается на сверхмощных печах, то длительность расплавления можно установить 30-35 минут и далее его сокращать, используя для этого кислородную продувку. Но мы считаем, что связанные с этим проблемы экономически себя не окупают и лучше вместо одной быстроходной, технологически ограниченной печи поставить две ДППТНП, но с возможностью проведения всех технологических периодов.
Большим преимуществом ДППТНП является возможность работы без «болота». При хорошо организованном процессе нагрева металла, что нам удалось сделать в ДППТНП, наличие «болота» ухудшает ее энергетические и экономические показатели, что естественно. «Болото» - это уже готовый металл, прошедший все стадии плавки, в том числе и высокотемпературные с повышенными тепловыми потерями. Его стоимость по сравнению с шихтой возрастает и на последующей плавке он сразу после завалки превратится в «козел» и в процессе плавки частично окислится. В зарубежных печах «болото» необходимо. Оно защищает подину печи от воздействия дуг и, ускоряя начало кислородной продувки, позволяет быстрее выходить на полную мощность, давая выигрыш во времени. В ДППТНП форсированное плавление можно вести сразу без «болота».
Для СДП серьезным путем увеличения их производительности и экономии электроэнергии явилось использование при плавках жидкого чугуна [1]. Очевидно, что в процессе плавления с кислородной продувкой его потери за счет угара соизмеримы с потерями металлической шихты, а эффективность получения стали из чугуна вряд ли эффективнее конвертора.
По технологиям ДППТНП переработку чугуна в сталь можно вести другими методами. Например, для Ярославского моторного завода мы поставили агрегат – дуговой миксер постоянного тока. Он состоит из двух тиглей емкостью 12 т, оснащен одним источником питания 4,5 МВА и имеет производительность до 40 т/ч. Агрегат предназначен для нагрева, регулирования химсостава, включая по углероду, глубокого обессеривания и раздачи чугуна, заливаемого в него из коксовых вагранок. Это оборудование можно эффективно использовать в сталеплавильном производстве по схеме – доменный процесс – миксер или доменный процесс – конвертор с незавершенным процессом окисления углерода – миксер. При этом окисление углерода в миксере мы предлагаем вести железнорудными окатышами, а не кислородом. Это позволяет увеличить выход стали за счет пригара, провести ее глубокое обезуглероживание, дефосфорацию, десульфурацию и легирование до любой заданной марки. Удельный расход электроэнергии не превысит 90 кВт·ч/т, а установленная мощность, например, для миксера емкостью 100 т и производительностью 200 т/ч – 25 МВА. Технологические возможности ДППТНП, описанные выше, без всякого сомнения, приведут и к очень существенному повышению качества металла.
Добавление жидкого чугуна в завалку ДППТП так же целесообразно, но окисление углерода кислородом следует тоже заместить окислением железной рудой совместно с шихтой, подаваемой в завалку. В этом случае вместо потери 8-10 % чугуна при окислении кислородом реализуется увеличение не менее чем на 15 % от массы завалки чугуна стали. В СДП эти процессы вести нельзя.
Универсальность ДППТНП, по нашему мнению, должна изменить отношение к формированию структуры плавильных отделений металлургических заводов. Если современная сверхмощная ДСП может провести расплавление и окислительный период с высокой скоростью, а затем из нее металл необходимо быстро перелить в печь-ковш, который является ее неотъемлемой частью, то в ДППТНП можно полностью сварить сталь, обеспечив высокий уровень ее качества и достаточно долго удерживать металл в печи без ухудшения его свойств в случае отказа какого-либо агрегата технологической линии. ДППТНП в отличие от других печей обеспечивает равномерность температуры металла во всем объеме расплава и позволяет точно установить ее величину. Это обеспечивает и заданный уровень температуры металла в ковше, позволяя отказаться во многих случаях от установки печь-ковш. Дуговой нагрев металла в ковше может только ухудшить свойства металла, тогда как запас температуры сливаемого из ДППТНП металла с заданным химсоставом и шлака высокого качества может обеспечить ведение обработки металла в ковше без энергоемких операций ковшовой обработки. Устранение интенсивного окислительного процесса создает условия для улучшения качества металла.
В ДППТНП для ускорения расплавления и экономии электроэнергии можно использовать кислород, газовые горелки и поскольку они в отличие от современных ДСП не являются жизненно необходимыми для ведения процесса плавки их воздействие можно регулировать в широких пределах, обеспечивая, например оптимальное соотношение экономии электроэнергии, угара металла, выбросов в окружающую среду, а затем вести дальнейшую доводку металла с использованием установок печь-ковш и делать это экономичнее, чем в других печах. Но мы считаем, что гораздо эффективнее вернуть в плавильные печи все стадии плавления и обработки расплава, добиться сокращения времени их ведения, и не ставить главной задачей весь металл плавить в одной печи, не обращая внимания на экономику процесса, экологию и надежность работы всего комплекса. В ДППТНП в этом направлении нам удалось добиться серьезных результатов.
В структуре стоимости основных фондов металлургического предприятия полного передела, доля плавильного отделения не превышает 20 %. В тоже время, в печи расходуется львиная доля энергоресурсов, формируются основные отходы производства, воздействующие на окружающую среду. Отказы плавильного оборудования останавливают все остальное производство. С учетом всего материала выше изложенного в докладе представляется, что для производства 200 т металла в час лучше установить две универсальные ДППТНП емкостью 100 т со временем плавки 60 минут в каждой, чем одну 100 т печь со временем плавки 30 минут и установку печь-ковш.
Технико-экономические преимущества ДППТНП.
ДППТНП, в отличие от других современных печей, сохранили использование электрической дуги в чистом виде и для своей работы не требуют привлечения других источников тепла. При анализе затрат на основные фонды главной статьей является более высокая стоимость источников электропитания ДППТНП, цена которых значительно снижается из-за возможности их производства в России. Однако при покупке СДП следует обращать внимание на стоимость всего комплекса оборудования, многие из единиц которого для ДППТНП просто не нужны или нужны в меньших объемах. Это системы пылегазоочитски, утилизации избыточного тепла, динамические фильтрокомпенсирующие устройства, силовые подстанции и линии электропередач повышенной мощности, газопроводы, кислородные станции высокой производительности, мощные шлакоотвалы и др. оборудование, территория для их размещения. Затраты на них много выше стоимости ДППТНП.
Возможность разработки новых технологий.
Мы видим большие возможности ДППТНП в создании новых высокоэффективных технологий и совершенствовании традиционных.
Такими перспективными направлениями мы считаем замену кислорода рудой при ведении окисления углерода чугуна, выплавку сталей из синтикома с использованием возможностей ДППТНП, выплавку стали из металлизованных окатышей, в том числе со сниженным коэффициентом металлизации, переплав низко, средне и высоко легированных сталей с сохранением после переплава легирующих элементов, разработку новых сплавов и марок стали с учетом новых возможностей оборудования, выплавку методом сплавления ферросплавов типа FеTi, FеAl, AlTi и др., реконструкцию с переводом на технологии НТФ «ЭКТА» парка ДСП, перевод на выплавку в ДППТНП сталей с повышенными требованиями к механическим свойствам – трубных заготовок, рельсов, сталей и сплавов специального назначения, широкое использование окалины для ведения восстановительных процессов.
Вызывает удивление реконструкция цехов с мартеновскими печами, при которой вместо кардинального решения вопроса плавки, связанного с заменой печей, цеха оснащают установками печь-ковш, затраты на которые соизмеримы с затратами на ДППТНП, позволяющие решить задачи реконструкции комплексно с расчетом на перспективу развития экономического и экологически чистого производства качественных сталей.
Еще большее удивление вызывает использование СДП в металлургическом машиностроении, в котором идет частая смена марок стали, чему мешает «болото», высокий, до 60-70 % возврат собственного производства, выжигание из которого металла и легирующих элементов резко увеличивает потери, и так как производство непрерывно не работает, эффективность СДП резко снижается. Действующие производства, как правило, находятся внутри жилых массивов, и на них оказывают мощное давление экологи. Установка СДП неминуемо значительно повысит себестоимость стали за счет значительных затрат на экологию, которые, в отличие от установки ДППТНП, не окупаются.
Выводы.
1. Технико-экономические и экологические преимущества ДППТНП подтверждены результатами их промышленной эксплуатации при выплавке стали, специальных сплавов на основе алюминия. Печи можно увидеть в работе. Так за период эксплуатации ДППТ-6АГ ОАО «Курганмашзавод» объединение посетили представители более 80 отечественных и зарубежных предприятий, и все они пришли к твердому выводу о необходимости срочной реконструкции своего плавильного оборудования путем установки ДППТНП. В настоящее время НТФ «ЭКТА» проводит и провела реконструкцию печей многих предприятий, таких как ОАО «Курганмашзавод», ОАО «Мотордеталь», ОАО «Рудгормаш», ОАО «ГАЗ», ОАО «Усольмаш», ОАО «Тяжпрессмаш», ОАО «Ижсталь», ОАО «Уралмашзавод», «Mardia Still», «Aluminium alloys of Estonia AS» и др. Длительное время работают наши печи емкостью до 32 т. Разработку крупнотоннажных печей емкостью до 80-100 т сдерживает только ориентация Заказчиков на зарубежные печи, вызванная в т.ч. слабой информированностью специалистов, связанной с оборудованием и технологиями ДППТНП.
2. Из приведенного материала следует, что замена ДСП на печи с комбинированными источниками тепла вызывает серьезные проблемы в энергоресурсосбережении и экологии и не может заменить работы по усовершенствованию дуговых печей.
3. Развитие технологии плавки в ДППТНП находится в начале пути и их возможности до конца не выявлены. Это подтверждают развитие новых технологий и совершенствование старых за счет расширения круга специалистов-металлургов производственников при введении на их предприятии новых печей. Их идеи являются базой для развития новых технологий.
4. Машиностроение России производит и готово расширить номенклатуру поставок ДППТНП любой емкости.
5. Разработки НТФ «ЭКТА» запатентованы в России.
Список литературы:
Хайссиг М., Фукс Г., Ауэр В. Технология производства стали в электродуговых печах в двадцать первом веке. V конгресс сталеплавильщиков (14-17 октября 1998 г., г. Рыбница).
Малиновский В.С., Дубинская Ф.Е. Технико-экономические и экологические аспекты плавки в дуговых печах постоянного тока. V конгресс сталеплавильщиков.
Малиновский В.С., Дубинская Ф.Е. Технико-экономические и экологические аспекты альтернативных технологий плавки металла в дуговых печах. «Электрометаллургия», №3, 1999 г.
Малиновский В.С. «Исследование и разработка мощных плазмотронов постоянного тока для плазменных плавильных печей». Диссертация на соискание ученой степени к.т.н., Москва, 1980 г.
Малиновский В.С. и др. «Требования к конструкции дуговой печи постоянного тока». «Металлургическая и горная промышленность», Днепропетровск, №4, 1988 г.
Закомаркин М.К., Липовецкий М.М., Малиновский В.С. «Дуговая печь постоянного тока емкостью 25 т. ПО «Ижсталь», «Сталь», №5, 1991 г.
Малиновский В.С. «Способ электроплавки и дуговая печь для его осуществления. Патент РФ № 2104450.
Малиновский В.С. «Способ электроплавки и дуговая печь для его осуществления. Патент РФ № 2048662..
Малиновский В.С. «Подовый электрод электропечи» Патент РФ № 2112187.
Афонакскин А.В. и др. «Результаты первого этапа освоения дугового плавильного агрегата постоянного тока нового поколения на ОАО «Курганмашзавод», «Литейное производство», №11, 2000 г.
Малиновский В.С., Ярных Л.В. «Дуговые печи постоянного тока нового поколения для металлургии машиностроения». «Металлургия машиностроения», №1, 2002 г.
Малиновский В.С., Ярных Л.В. «Дуговые печи постоянного тока в сталеплавильном производстве». Труды VI Конгресса сталеплавильщиков.
Дубинская Ф.Е. и др. «Уменьшение пылегазовых выбросов их электросталеплавильных печей постоянного тока». «Сталь», №9, 1991 г.
Дубинская Ф.Е. и др. «Современные тенденции очистки газов сталеплавильных печей». ЦИНТИТЭХИМ, «Промышленная и санитарная очистка газов». Серия ХМ, Москва, 1990 г.